AUTOMOTIVE
2023.12.19 | Updated: 2023-12.29
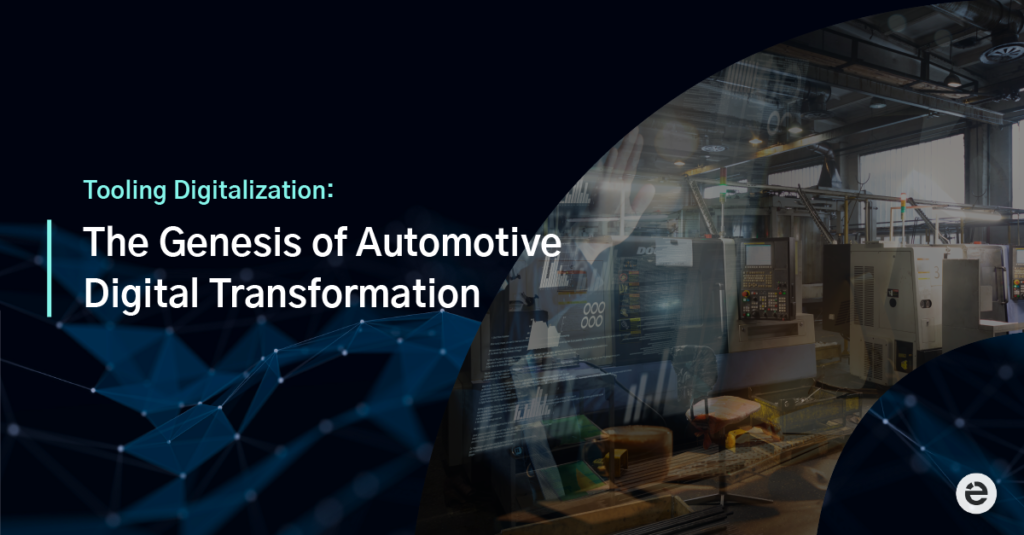
Tooling is the backbone of the automotive manufacturing industry, underpinning the entire production process. This foundational role of tooling, encompassing the myriad tools, molds, and dies, makes it a strategic starting point for digital transformation for the automotive industry. When companies embark on tooling digitalization, they immediately unlock benefits. Predictive maintenance, data-driven decisions, and cost savings become tangible outcomes, clearly demonstrating digital transformation’s value. This not only reduces downtime and waste but also amplifies production efficiency.
The Evolution of Automotive Manufacturing: A Glimpse
From Henry Ford’s assembly lines to the precision of today’s AI-driven analytics, automotive manufacturing has consistently been at the forefront of innovation, and each period introduced unique challenges, invariably with technological solutions that redefined production paradigms. As the digital age introduced interconnectedness and real-time analytics, the automotive industry was on the cusp of a new frontier. While initial efforts focused on CAD designs and automated robotics, the future hints at a more profound, holistic digital integration.
Understanding Tooling Digitalization
Tooling digitalization synergizes manufacturing with the prowess of digital technology. Pioneers like eMoldino exemplify this convergence by leveraging wireless IoT sensors and sophisticated software. Infused with AI and ML capabilities, these sensors transcend mere data logging; they’re the vigilant sentinels of the manufacturing floor, consistently delivering real-time insights. This synergy of hardware and software is reimagining the manufacturing blueprint.
Learn More Through Our Upcoming Online Webinar
The Strategic Advantages
Predictive maintenance: Predictive maintenance is emerging as a game-changer for the automotive industry. With tools and technologies that can anticipate tool failures and extend tool life by understanding pattern change, the benefits are profound:
- Global automotive and Fortune Global 500 industrial organizations can achieve annual savings of 1.6 million hours of downtime.
- These organizations could realize productivity gains amounting to $734 billion through a 6% increase in efficiency.
- Maintenance expenses can be cut by 40%, leading to cost reductions of $236 billion.
- OEMs can proactively rectify tooling issues, reducing unplanned downtimes.
Data-driven Decision Making: The digital era brings forth the power of data, transforming how companies operate and make decisions. Tooling digitalization is not just a mere operational upgrade; it’s a strategic compass offering:
- Insights play a pivotal role in tooling management, enabling the identification of tooling at risk of being lost or misplaced.
- Optimization of tooling utilization ensures that each tool is used to its fullest potential.
- Companies embracing data-driven procedures report enhanced productivity, informed decision-making processes, reduced operational costs, and improved product quality.
Cost Savings: With an emphasis on resource optimization and minimizing waste, organizations can unlock substantial cost benefits:
- Adopting predictive maintenance practices alone promises significant monetary savings, primarily from reductions in unplanned downtimes.
- Data insights further facilitate a leaner approach to inventory management.
- As organizations shift towards data-driven operations, there’s an inherent reduction in resource wastage and redundant practices, leading to considerable cost savings.
However, the implications of tooling digitalization extend beyond immediate operational gains. With the integration of IoT sensors and AI-driven analytics, a wealth of data is generated. This data, detailing tooling performance and efficiency, becomes the cornerstone for broader digital initiatives. As companies harness this data, they gain insights to streamline the supply chain. Monitoring parts production in real-time and optimizing supply interactions become achievable, transforming the once complex web of supply chain interactions into a streamlined, efficient process.
Companies prioritizing tooling in their digital journey set a precedent for subsequent digital initiatives. The digital evolution, when combined with the tangible benefits of tooling digitalization, not only highlights it as a technological endeavor but also establishes it as a strategic linchpin in the digital transformation journey of the automotive industry.
Register your free spot in this upcoming webinar to learn more from industry experts about how tooling digitalization is transforming automotive manufacturing and beyond
Explore Our Related Posts
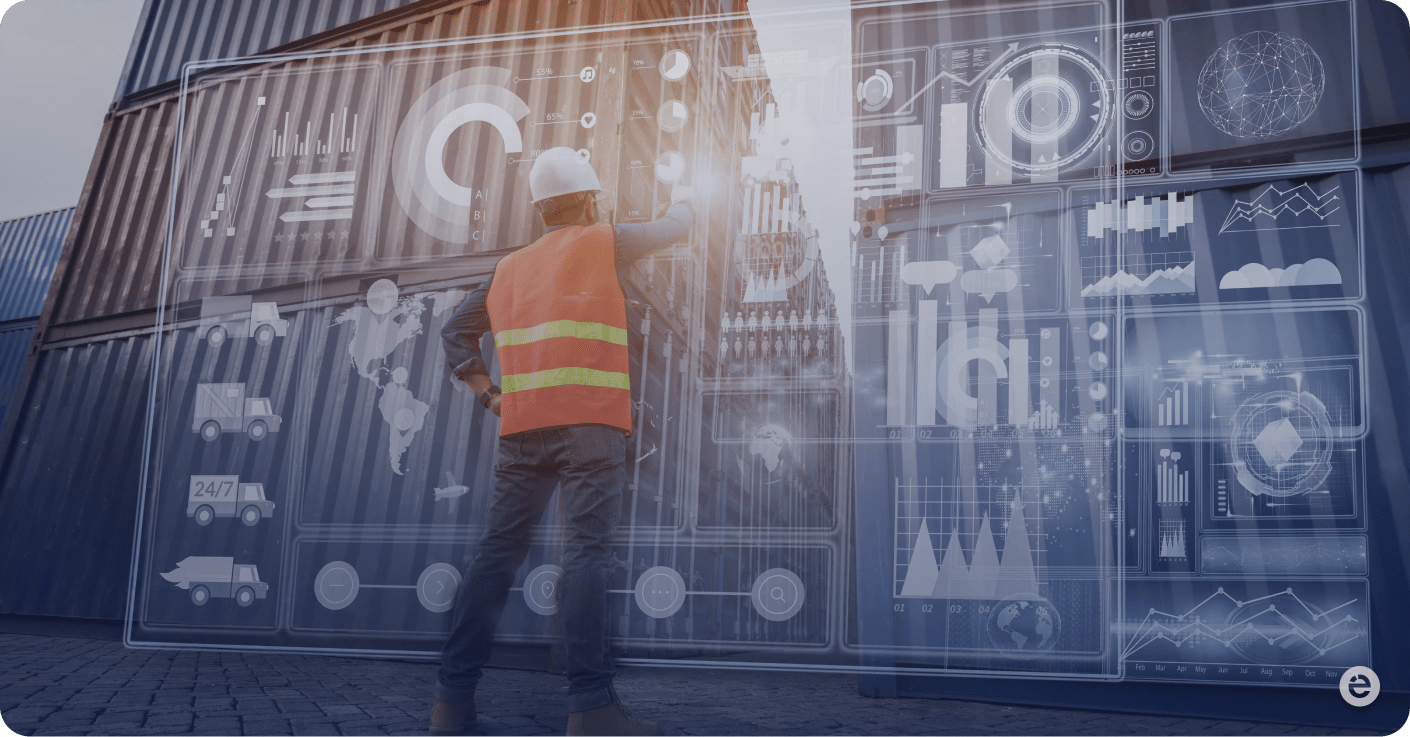
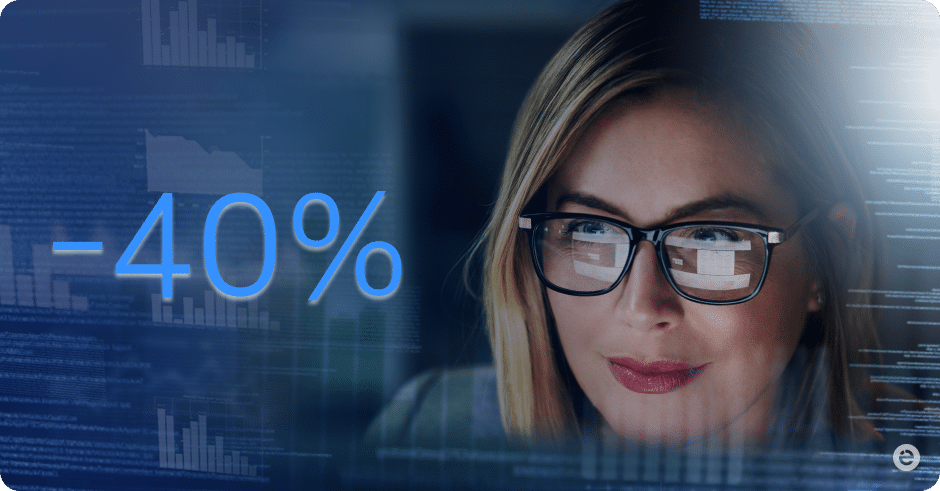

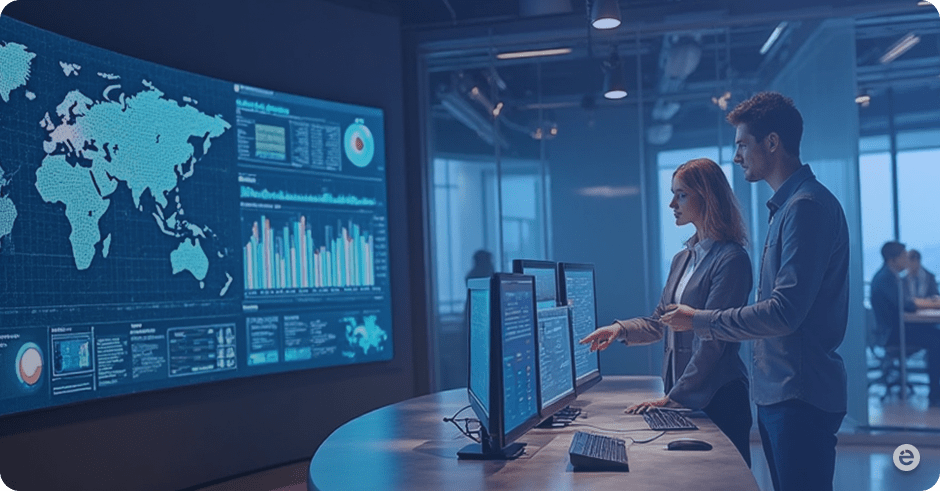
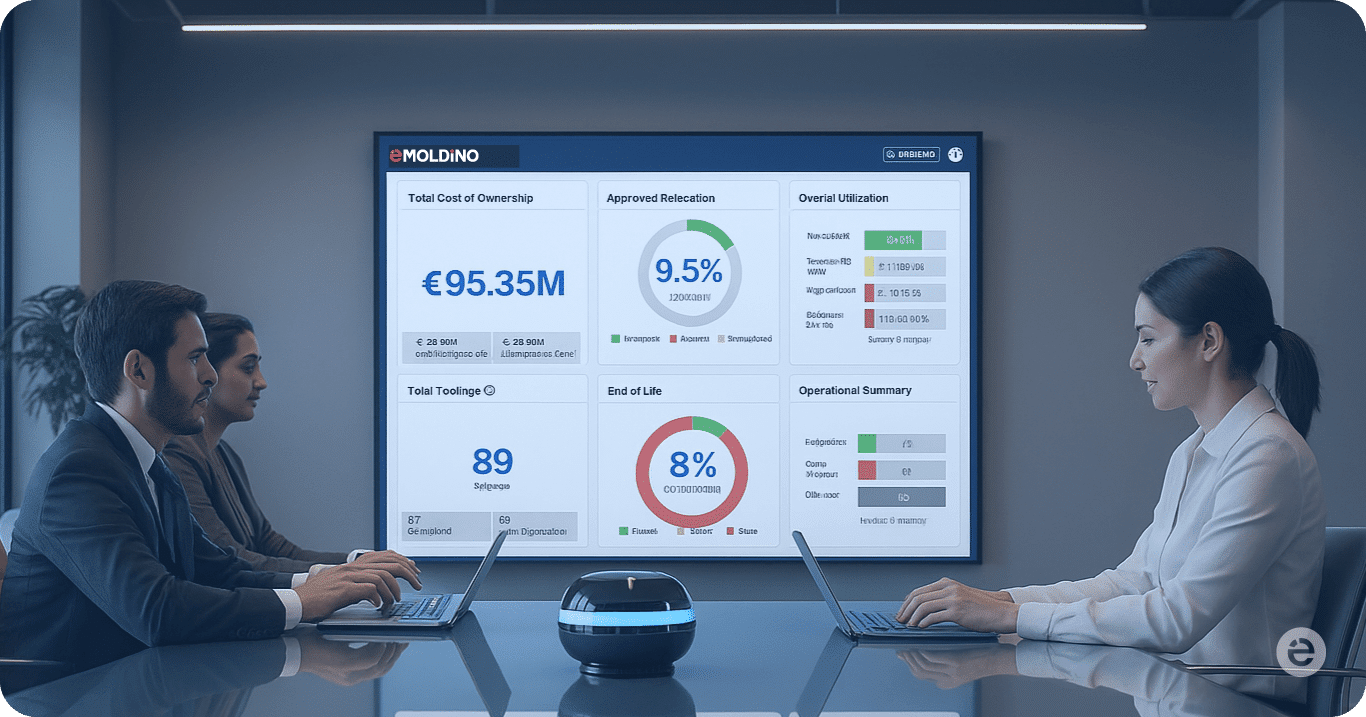
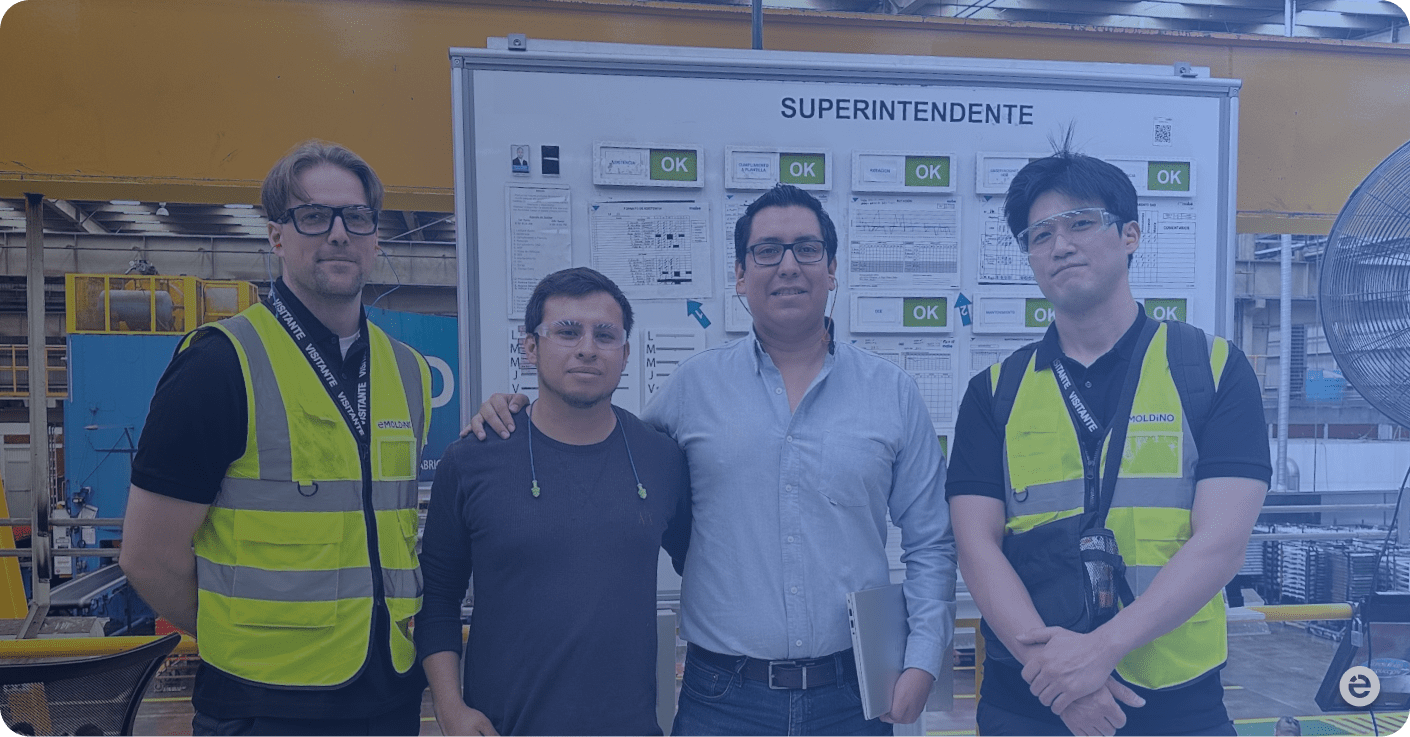
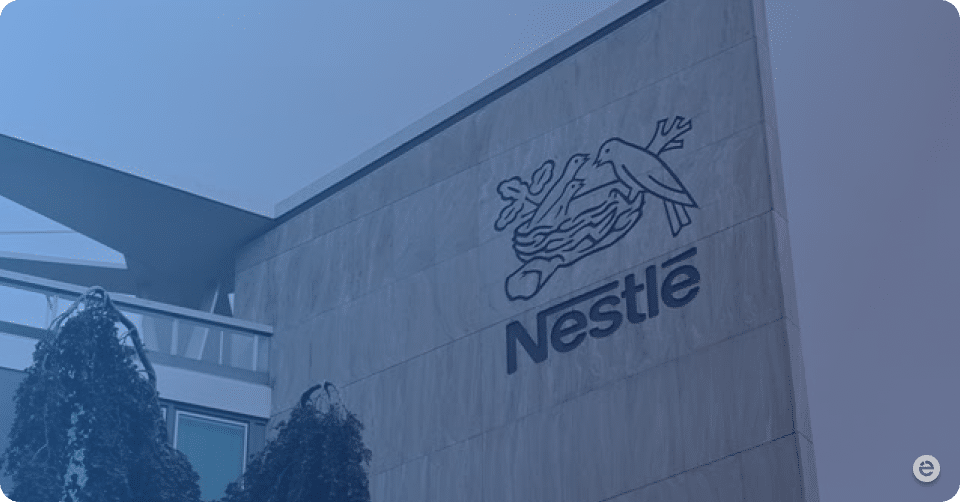
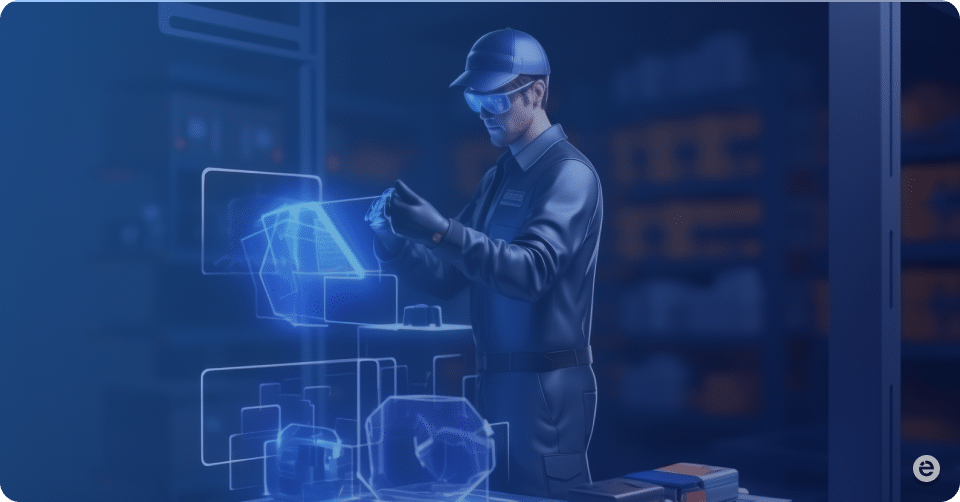
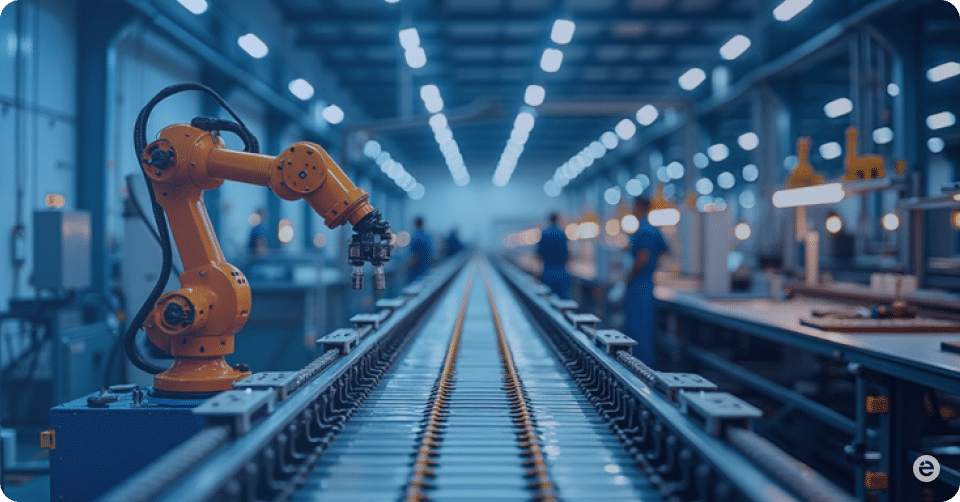
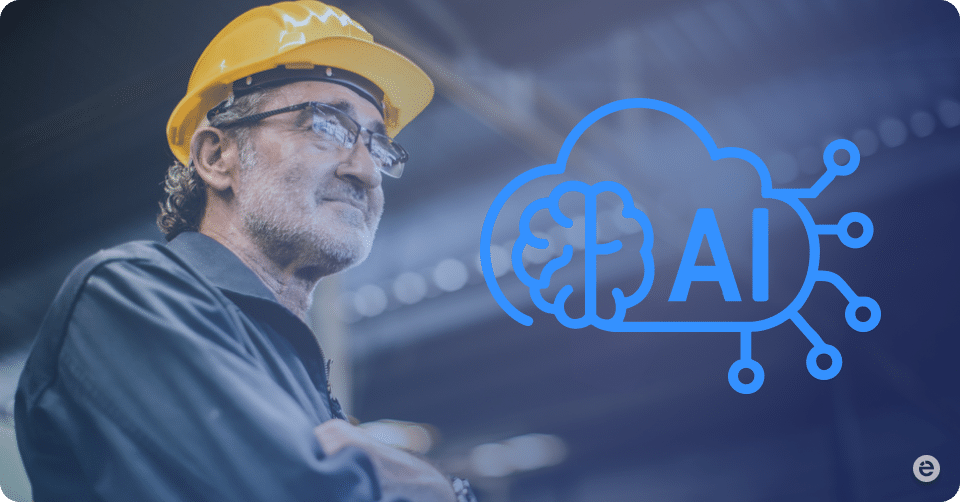