“Late part deliveries from suppliers frequently incur higher costs, particularly in our automotive sector, often necessitating expedited shipments to meet deadlines.”
– A Global Automotive Supplier.
“We have recently experienced supply disruptions resulting in temporary production stoppages”
– An Automotive Leader.
What’s the root of the issue?
At its core, the problem is straightforward:
Although many automakers have made strides toward digital transformation within segments of their operations, the majority have yet to embrace technology expertise fully.
The underlying issue is a need for comprehensive technology adoption across the industry, leading to significant information gaps during crucial phases like diecasting. This disconnect results in delivery delays, supplier risks, and financial losses. Executives often consider purchasing additional tooling or diversifying suppliers to counter shortages and ensure quality. With the high costs associated with downtime and failing to meet production targets, having clear visibility into production data becomes essential.
Solutions like real-time capacity planning tools have shown promises, with successful implementations leading to considerable cost savings and operational improvements.
“We’ve faced capacity issues and need real-time supplier capacity insights from a reliable source. Previously, we relied on potentially manipulated data. Real-time transparency is critical for strategic decisions. Suppliers provide manual data via Excel, which requires verification against real-time data through advanced technology.”
– A global automaker.
The value
Executive leaders recognize value in streamlined operations, cost savings, and enhanced revenue opportunities. Technological innovations, like sensor integration, are vital to improving supply chain efficiency and minimizing delays, leading to significant savings and better customer relationships.
Clients’ use cases
An automotive supplier needed more real-time insight into tooling capacity. This necessity arose from recurrent challenges with suppliers who frequently missed delivery deadlines, forcing the company to incur additional costs. To comply with production timelines, expediting materials via air transport, a particularly prevalent solution within the automotive sector, became a routine practice. They implemented sensors across their tools to better align their supply chain with demand planning. This strategic move reduced late deliveries and unexpected tooling breakdowns, saving $25.25 million.
Another automotive giant faced challenges due to insufficient real-time data on production output and available alternative suppliers or production sites. This information gap led to frequent late deliveries and shortages of promptly supplied parts. Adopting a tooling digitalization solution enabled the company to manage capacity and mitigate delivery risks effectively. By implementing sensors to monitor production and identify alternate supply chains, the company realized savings of €196,000. These instances underscore the importance of leveraging technology for cost efficiency and improved operational output.
Conclusion
Many automotive companies note the risk of supply disruptions from relying on single-source suppliers due to factors like labor issues or public crises, which could potentially impact production and financial health.
How can executives mitigate these risks and ensure production continuity?
About the author
eMoldino
eMoldino aims to digitalize, streamline, and transform your manufacturing and supply chain operations. We help global manufacturers who want to drive corporate innovation while maintaining the core values of collaboration and sustainability. Talk with us to learn more →
Did you enjoy reading this article?
4.4 / 5. Vote count: 5
Explore Our Latest Posts
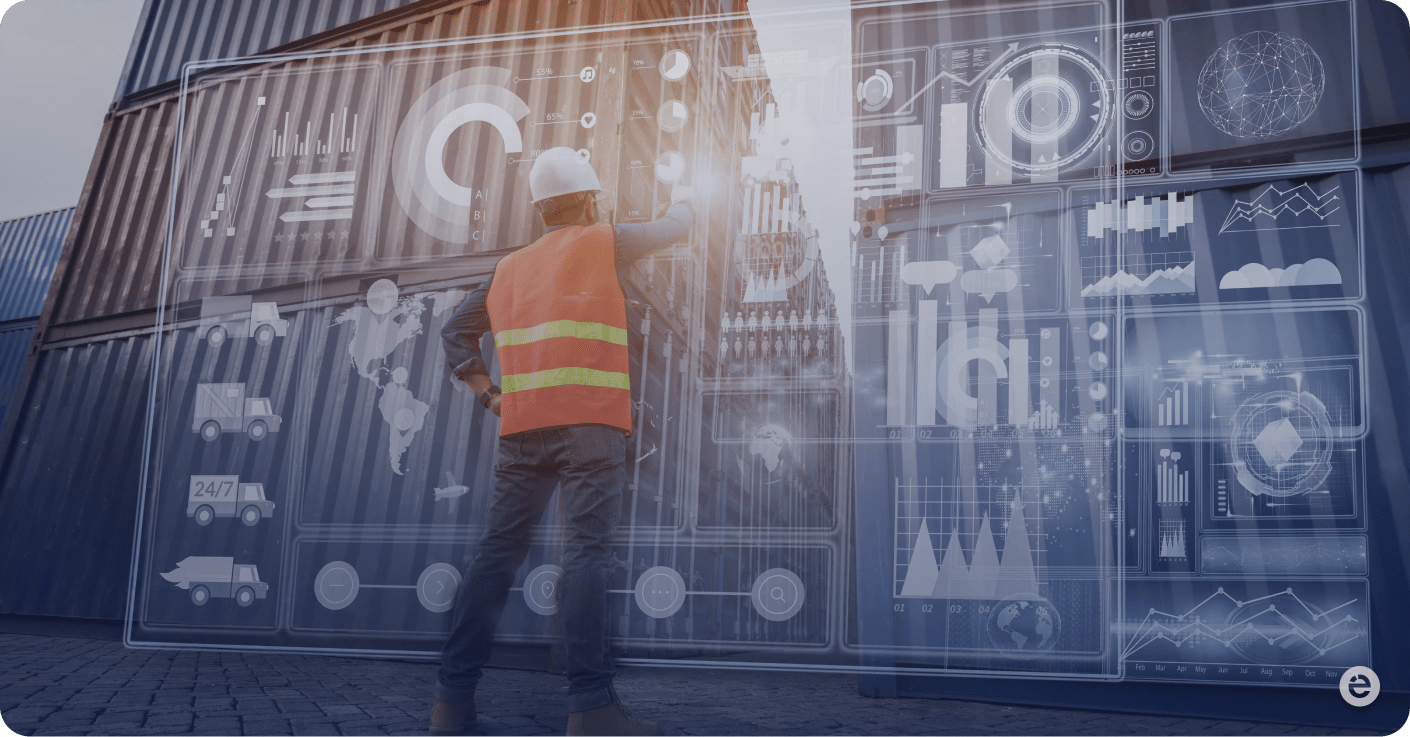
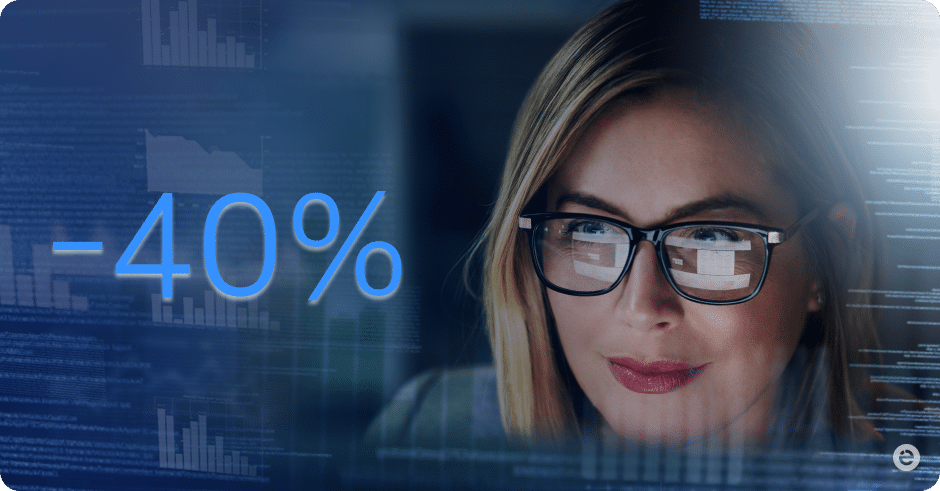

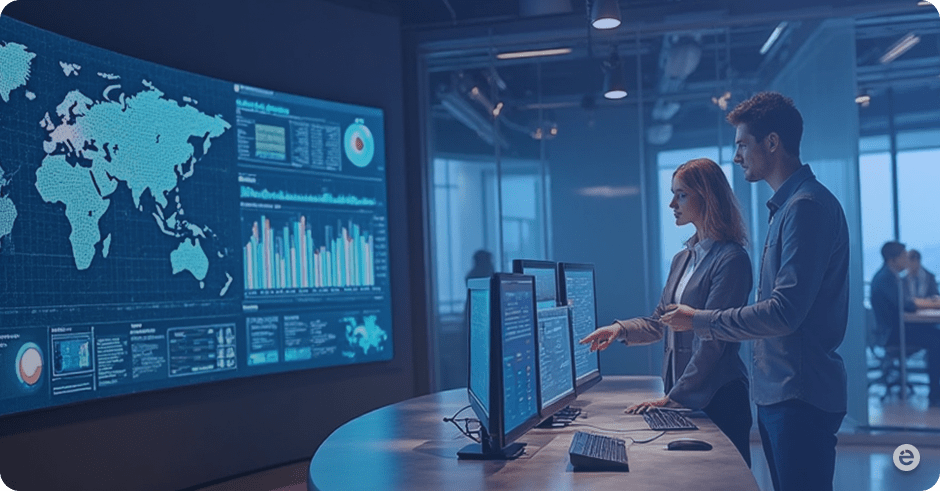
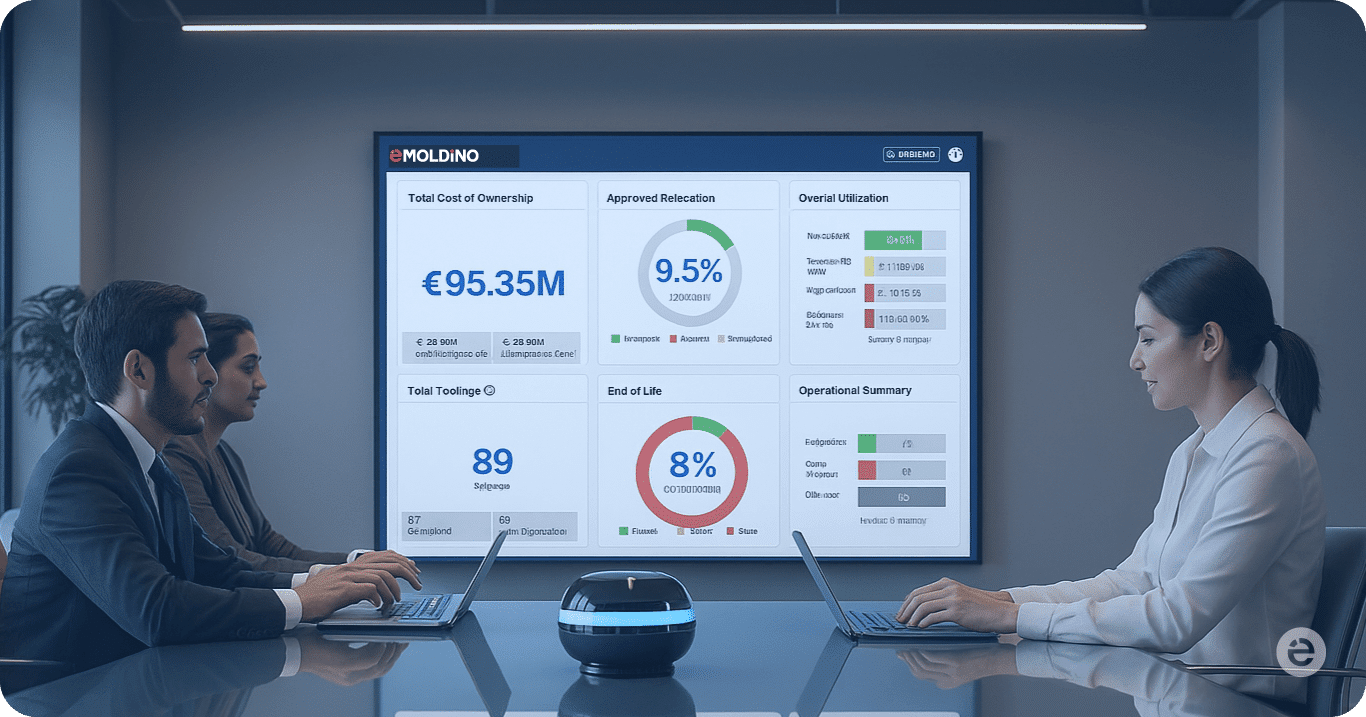
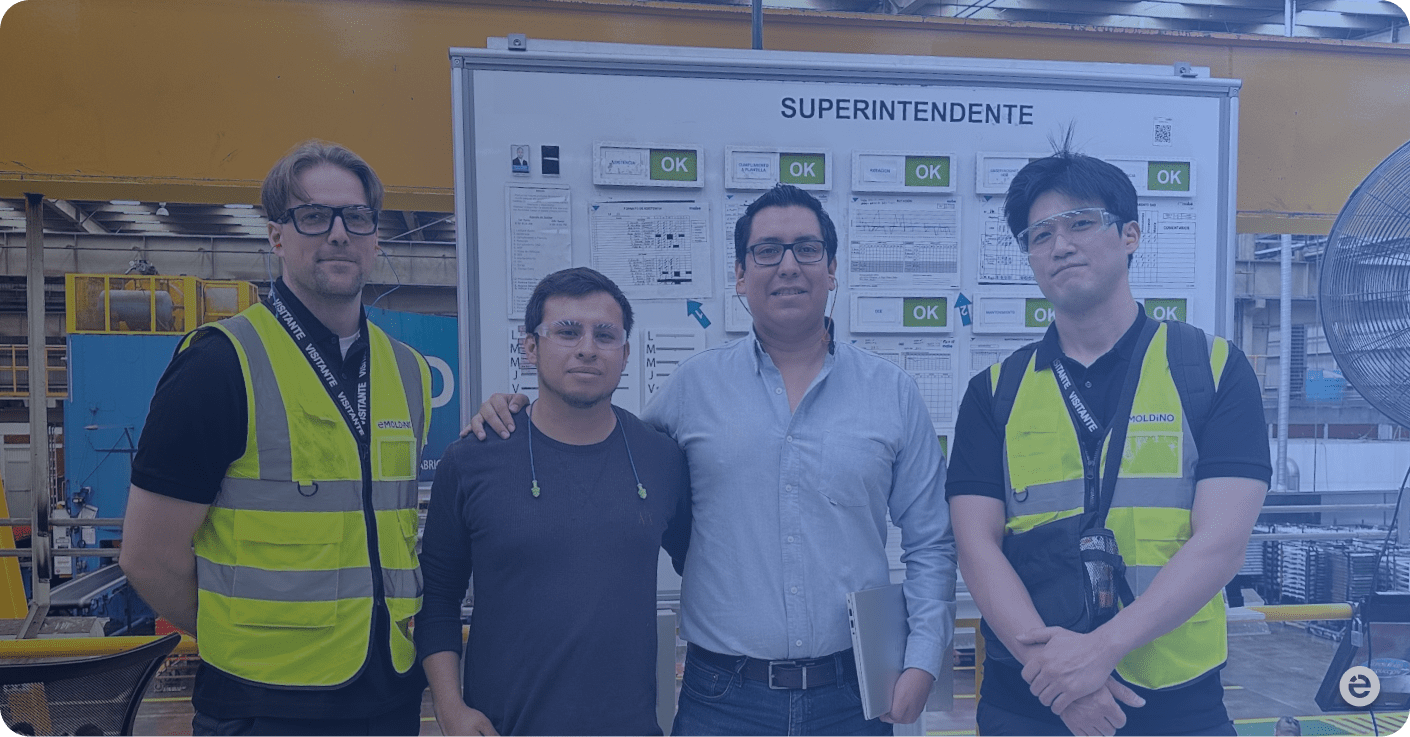
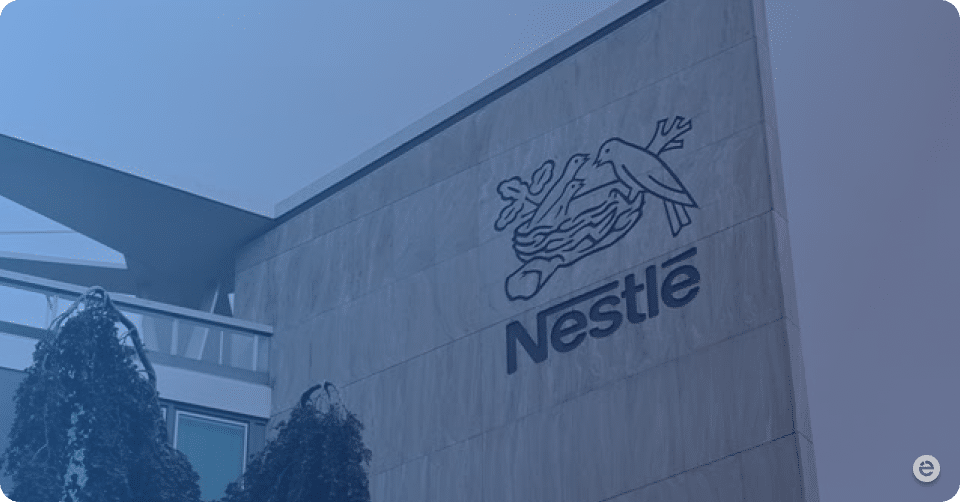
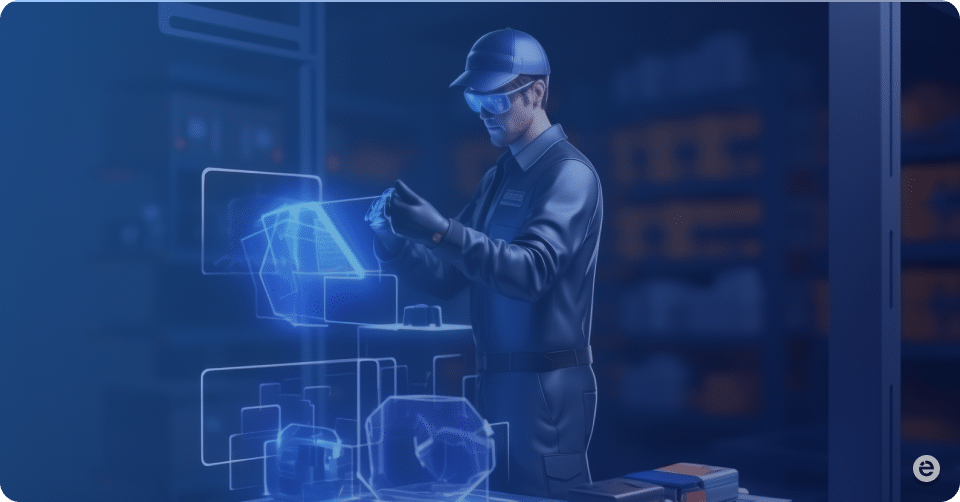
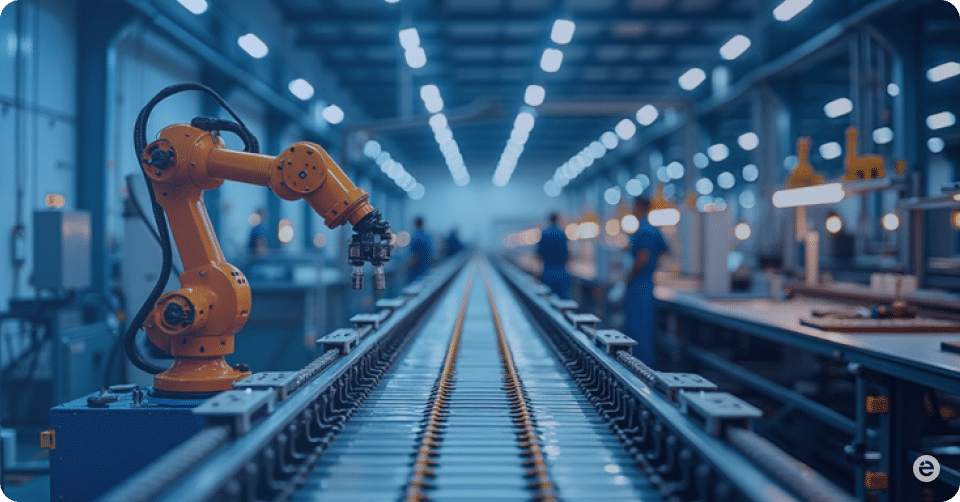
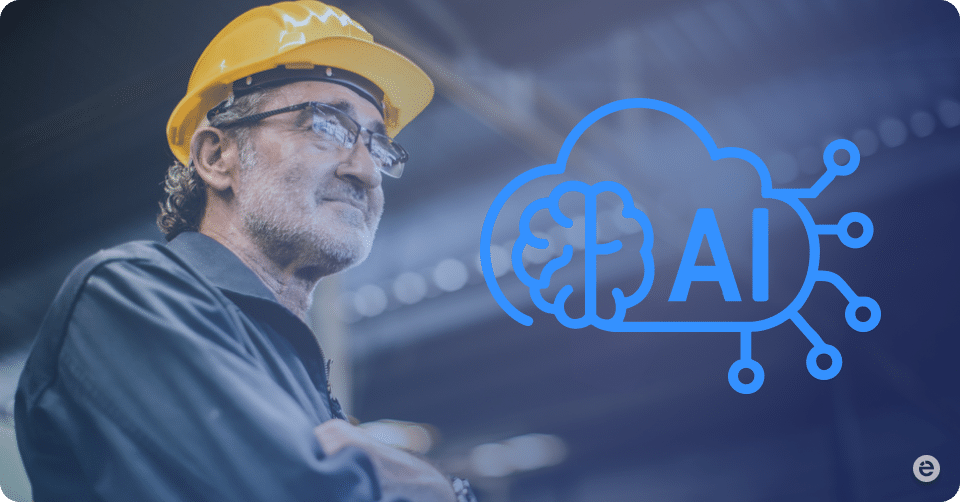