Introduction
Dans la fabrication externalisée, la gestion des taux de rebut est essentielle pour maintenir la rentabilité et l'efficacité opérationnelle. Des taux de rebut élevés font grimper les coûts et mettent en évidence des inefficacités qui compromettent la qualité, la capacité et la rentabilité des produits. Comment les technologies numériques peuvent-elles jouer un rôle essentiel dans la réduction des taux de rebut, l'amélioration de la visibilité opérationnelle et l'amélioration de l'efficacité de la production ?
Le rôle de la numérisation de l'outillage dans la réduction des déchets
Les outils numériques sont essentiels pour réduire les taux de rebut dans tous les secteurs de la fabrication. Les capteurs IoT d'eMoldino jouent un rôle central en permettant de surveiller et d'ajuster en temps réel les outils de production. Cela permet de réduire la variabilité et de minimiser les défauts dans les processus de production. Les transformations numériques améliorent la prise de décision, rationaliser la productionet de soutenir la compétitivité grâce à une intégration technologique stratégique. Selon McKinsey & Company, de telles intégrations peuvent conduire à des réductions de coûts de 5 à 7 % par mois en éliminant les goulets d'étranglement de la production et en améliorant l'efficacité globale des processus. (McKinsey & Company).
Cas concret
En mai 2022, une grande entreprise automobile a lancé un projet pilote avec des experts en numérisation de l'outillage. les inefficacités de production chez deux fournisseurs clés. L'accent a été mis sur le moulage sous pression de l'aluminium (HPDC), un processus essentiel à leur fabrication, mais affecté par un taux de rebut élevé et des divergences opérationnelles.
À HPDC, le contrôle insuffisant des températures de préchauffage des moules a entraîné des taux de rebut excessifs, des coûts de production élevés et une perte de capacité de production. Les principaux défis à relever sont les suivants :
- Données insuffisantes sur l'outillage : Cela signifie que les premiers signes d'usure de l'outillage et les défaillances imminentes n'ont pas été détectés.
- Faible visibilité : Le suivi de la production en temps réel présentait des lacunes importantes, ce qui rendait difficile l'identification des cas où les opérations s'écartaient des paramètres fixés.
- Analyse des causes profondes : Le manque de visibilité opérationnelle détaillée a entravé la capacité à diagnostiquer et à traiter efficacement les causes sous-jacentes des inefficacités.
Pour relever ces défis, l'entreprise automobile s'est appuyée sur une solution avancée de numérisation de l'outillage, avec des capteurs spécialisés qui surveillent la température extérieure de l'outillage, en suivant efficacement les temps de préchauffage et les écarts de température, ce qui lui permet d'avoir une vue d'ensemble de l'outillage :
- Meilleure visibilité de l'efficacité de l'outillage : Les données en temps réel sur les performances de l'outillage ont permis d'identifier les pertes d'efficacité et les améliorations potentielles.
- Suivi des capacités et de la qualité : Le contrôle continu de la capacité de production et de la qualité des pièces a permis de détecter les écarts et de les corriger rapidement, réduisant ainsi les risques de rebut.
- Des informations fondées sur des données : L'intégration d'une analyse complète des données relatives à l'outillage a facilité la maintenance proactive et les ajustements opérationnels, réduisant ainsi les temps d'arrêt et améliorant la qualité de la production.
La mise en œuvre de la solution de numérisation avancée de l'outillage a révélé que les fluctuations de température quotidiennes coûtaient 5 minutes de production par jour. Bien que ces fluctuations ne représentent que 0.3% du cycle de production, ils ont produit 4 181 pièces défectueuses par outil et par an, de 1 200 000 pièces. Financièrement, cela s'est traduit par un coût important, chaque pièce défectueuse coûtant $5, soit un montant cumulé de $20 906 perdues par outil chaque année en raison de pièces défectueuses. Pour 3 000 outils, ce problème s'est traduit par une perte annuelle combinée de 1,5 milliard d'euros. $62,718,000.
Le projet pilote a permis de réaliser des économies substantielles en réduisant les déchets et a renforcé la valeur du suivi des données en temps réel dans la rationalisation des processus de fabrication.
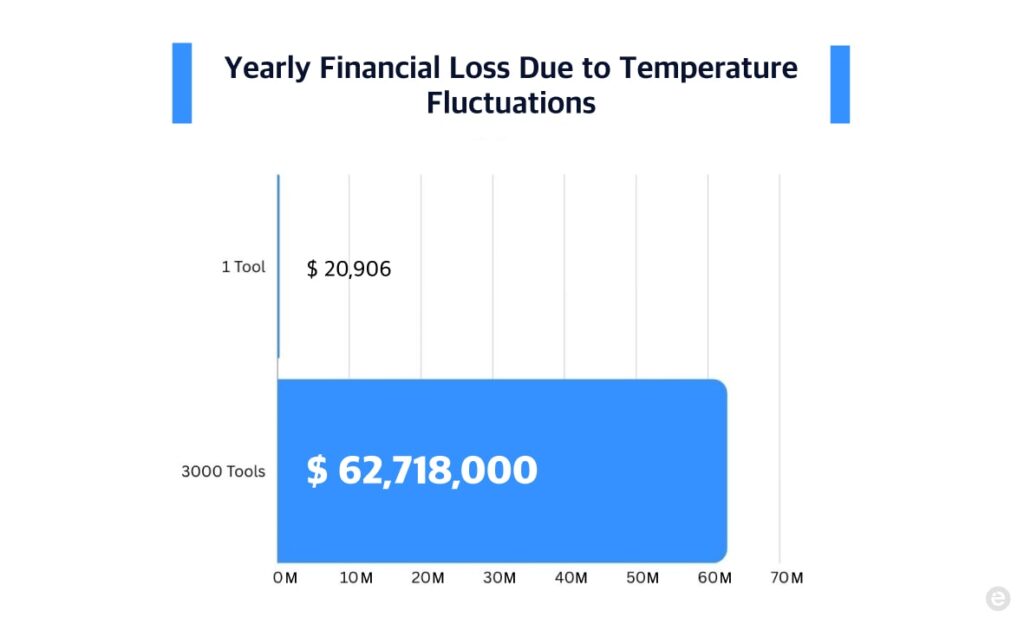
Conclusion
Les chefs d'entreprise avant-gardistes ne se contentent pas de considérer les taux de rebut et l'inefficacité des processus comme des obstacles à surmonter ; ils voient dans ces défis des possibilités d'amélioration substantielle et de différenciation stratégique. Plutôt que de se contenter d'atténuer les inefficacités, les entreprises visionnaires profitent de cette période pour mettre en œuvre de profondes transformations numériques. Votre entreprise est-elle prête à adopter la numérisation des outils et l'analyse des données en temps réel pour améliorer sa résilience opérationnelle ?
A propos de l'auteur
eMoldino
eMoldino a pour objectif de numériser, de rationaliser et de transformer vos opérations de fabrication et de chaîne d'approvisionnement. Nous aidons les fabricants internationaux qui souhaitent stimuler l'innovation au sein de l'entreprise tout en maintenant les valeurs fondamentales de collaboration et de durabilité. Discutez avec nous pour en savoir plus →
Avez-vous apprécié la lecture de cet article ?
4 / Le décompte des voix : 1
Découvrez nos derniers articles
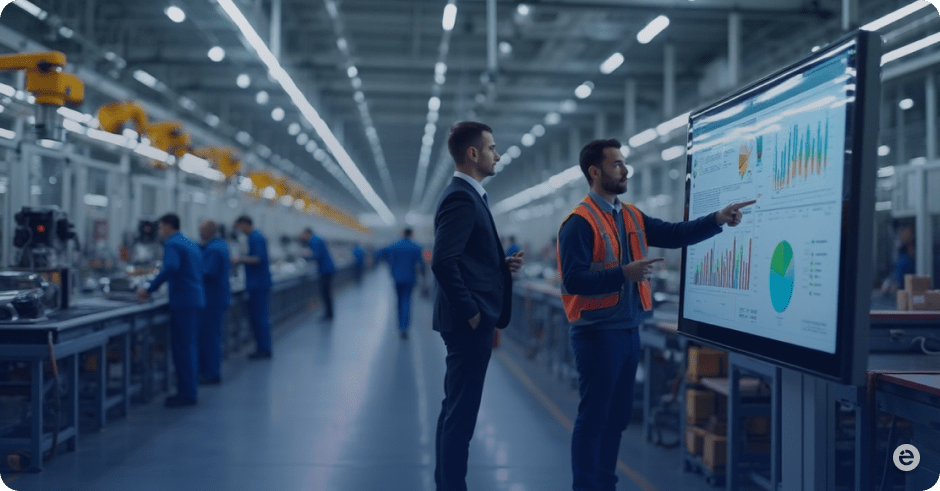
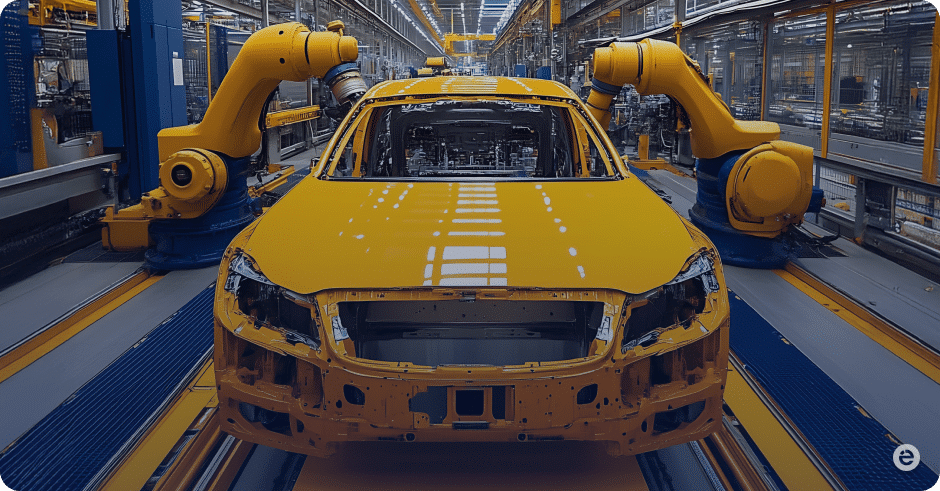
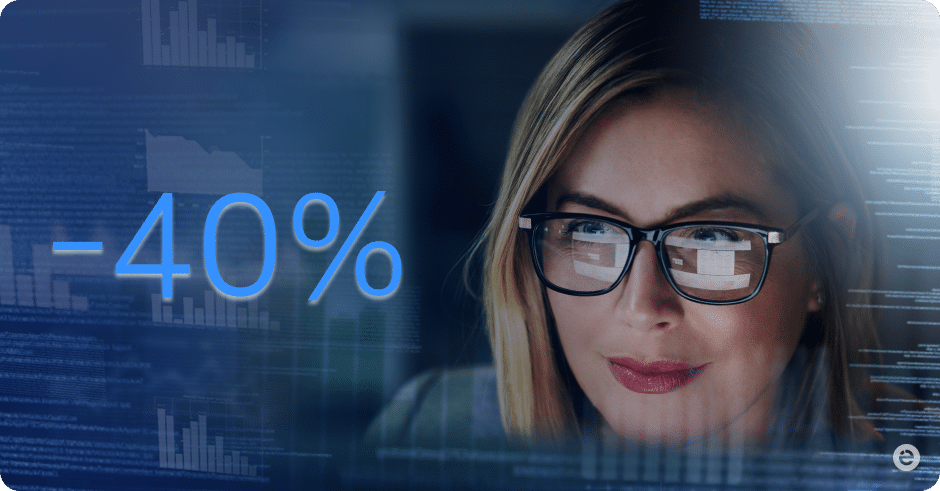
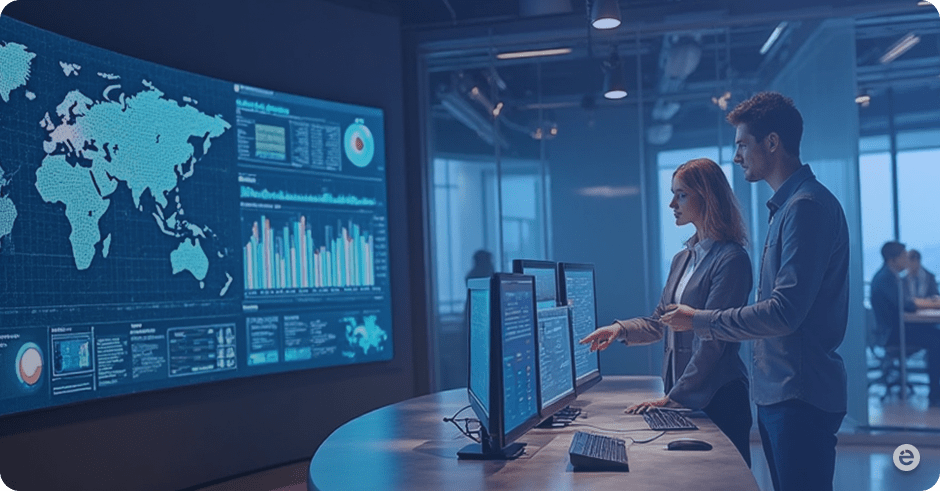
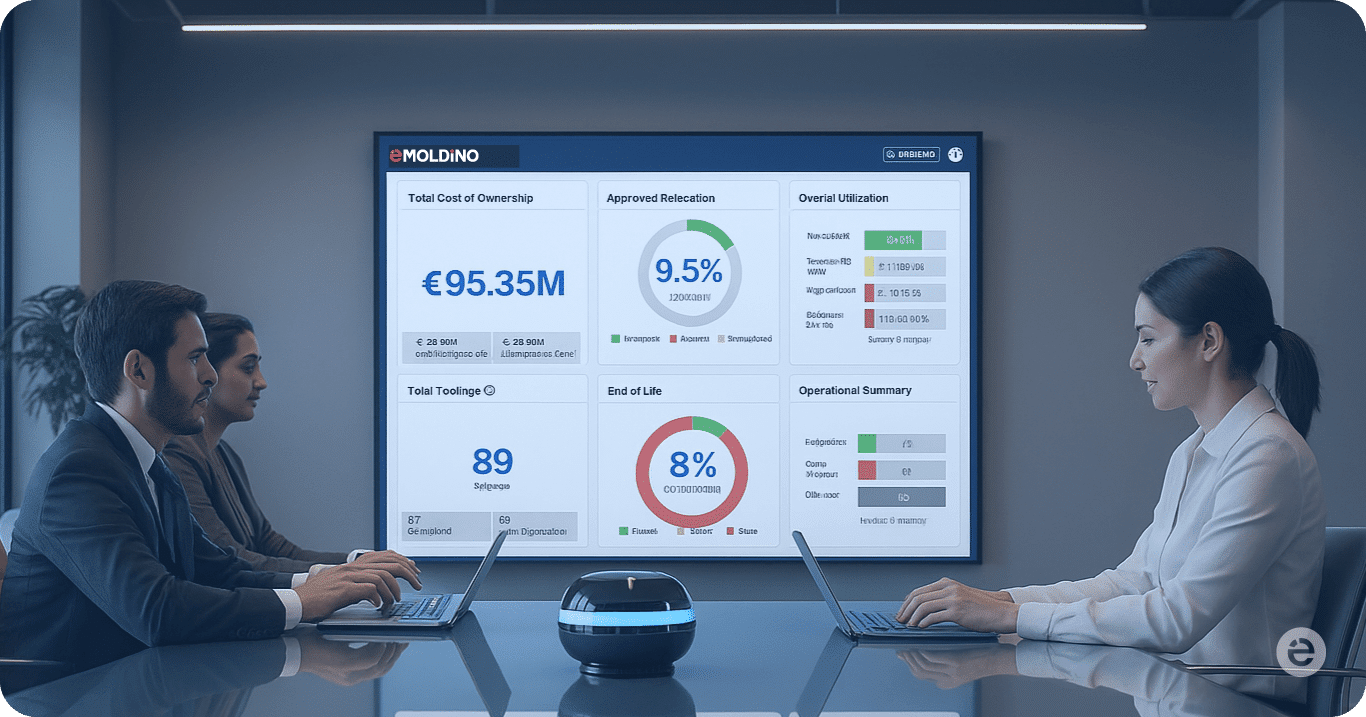
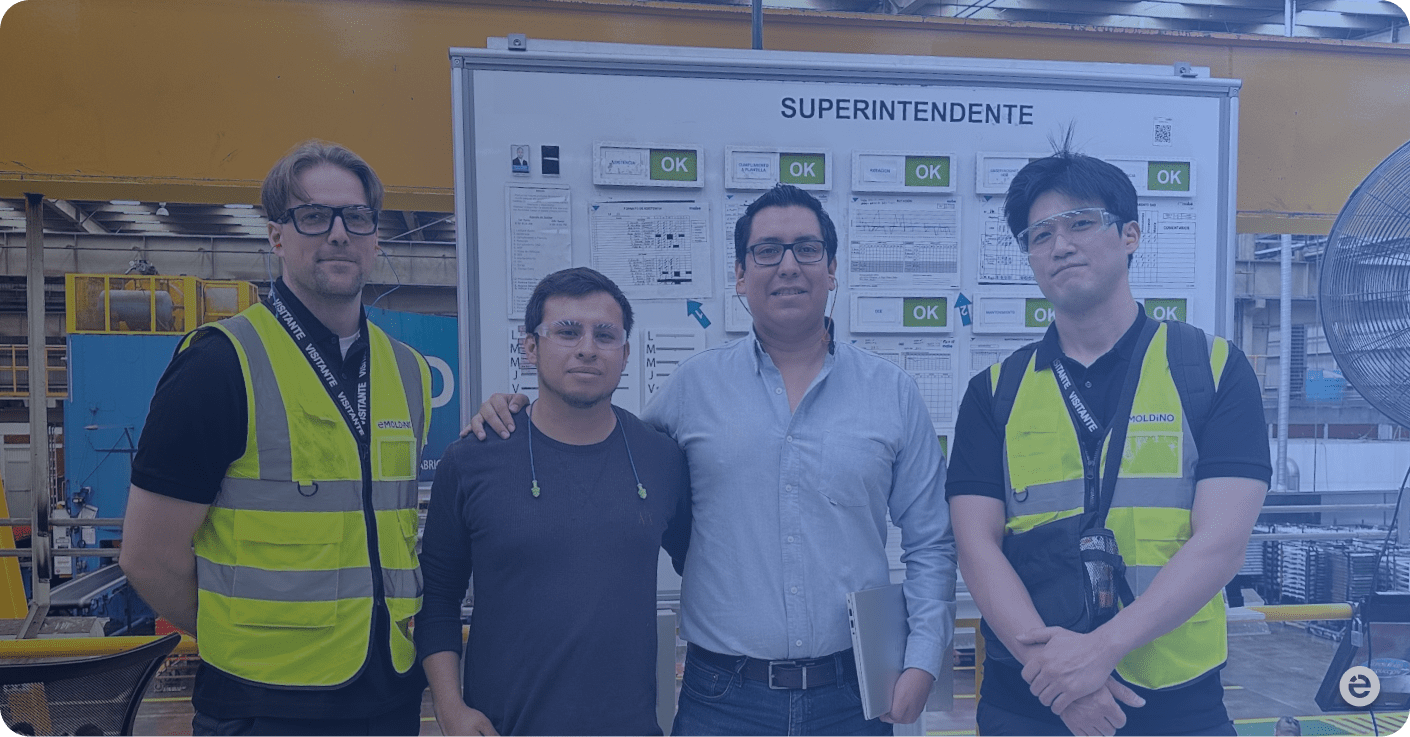
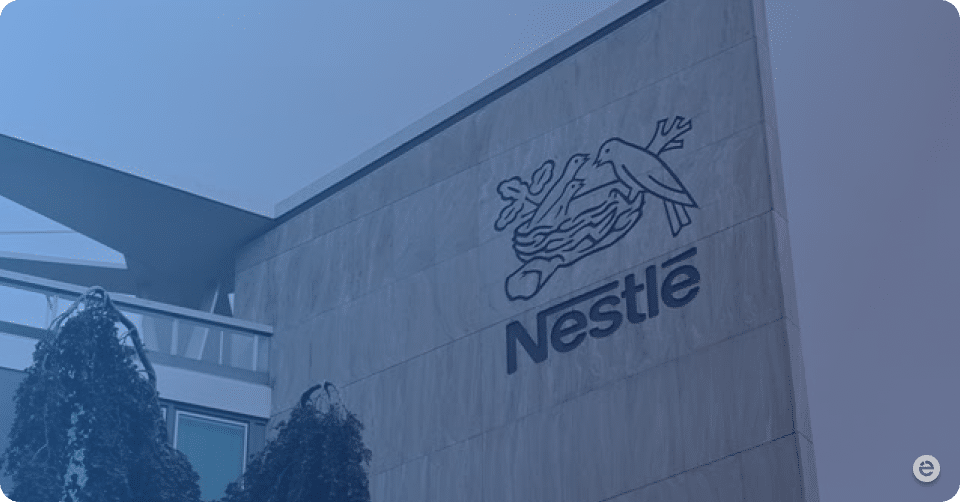
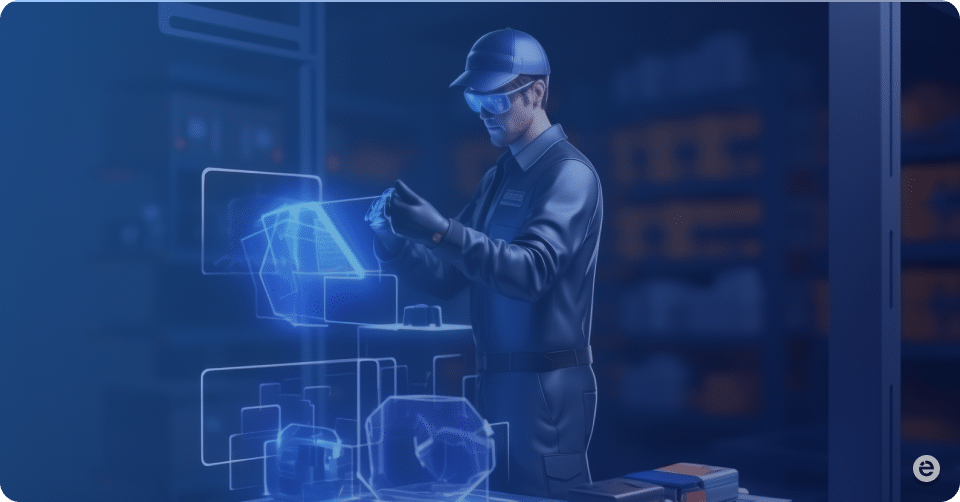
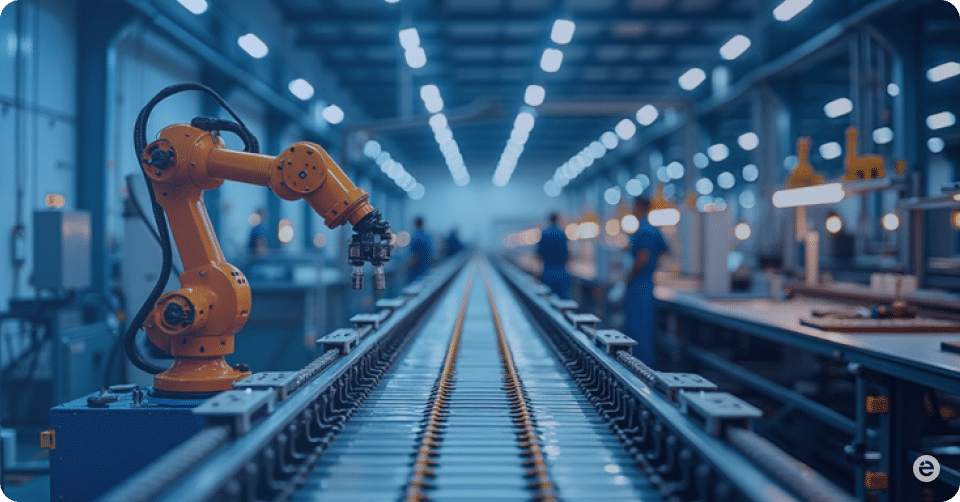
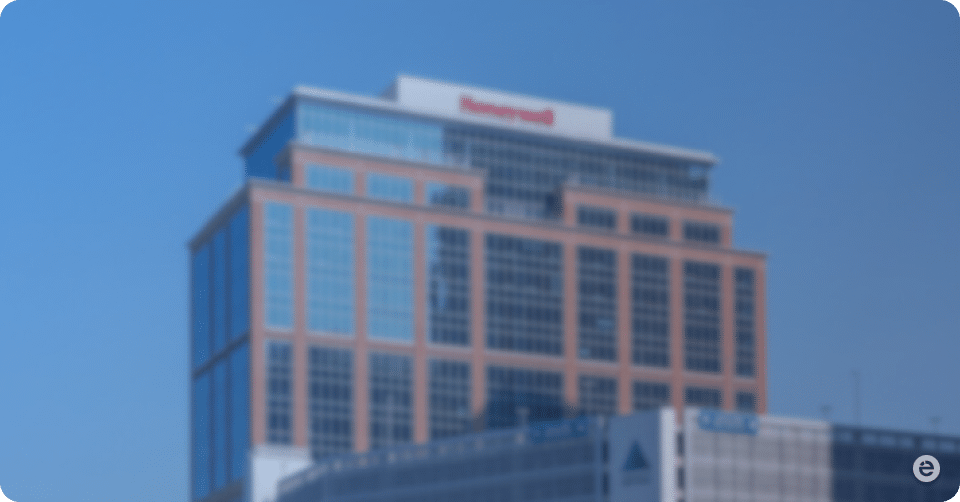
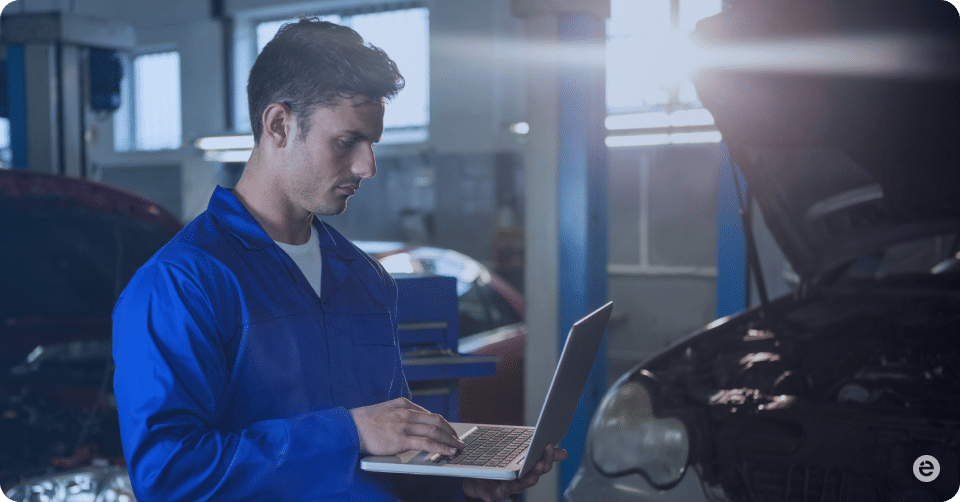