AUTOMOTIVE
2023.12.19 | Aktualisiert: 2023-12.29
Konvergenz von Werkzeugdigitalisierung und nachhaltiger Fertigung
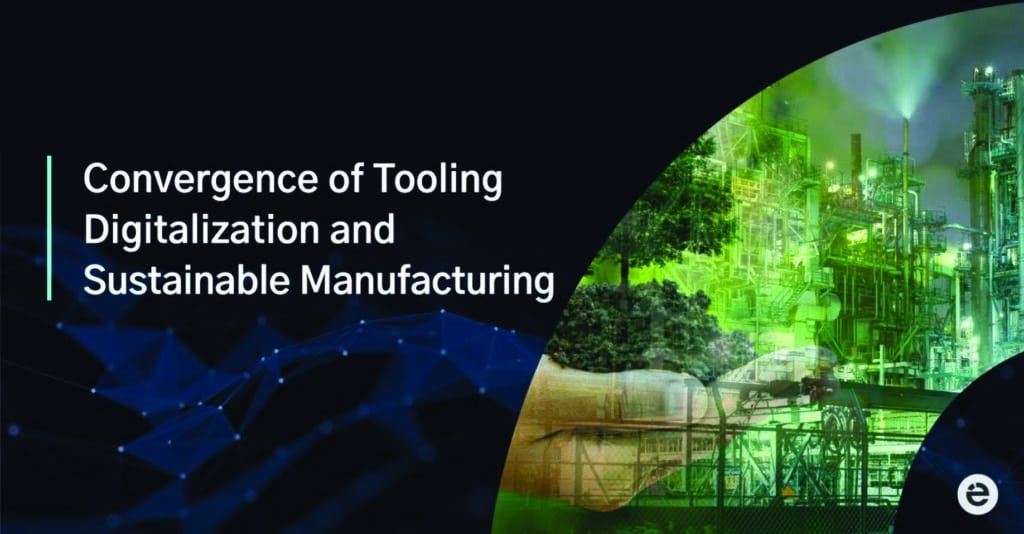
Angesichts der zunehmenden Besorgnis über Umweltprobleme setzen verschiedene Branchen, darunter auch die Automobilindustrie, auf eine nachhaltige Fertigung, um ihren CO2-Fußabdruck zu verringern und ihre Wettbewerbsfähigkeit zu erhalten. Ein vielversprechender Ansatz, der an Dynamik gewinnt, ist die Konvergenz der Digitalisierung von Werkzeugen mit nachhaltigen Praktiken. Dieser Wandel hat erhebliche Auswirkungen auf eine Branche, die ihre Nachhaltigkeitsinitiativen verbessern möchte. In diesem Artikel wird das transformative Potenzial einer solchen Konvergenz untersucht, indem eine innovative Lösung für die Automobilindustrie vorgestellt wird, die auf dem Weg zu betrieblicher Exzellenz und einem verstärkten Engagement für die Umweltverantwortung voranschreitet.
Die Macht der Konvergenz: Integration von Technologie und Nachhaltigkeit
Die Digitalisierung ist ein wesentliches Element zur Förderung einer nachhaltigen Produktionsumgebung
Die Konvergenz von Werkzeugdigitalisierung und nachhaltiger Fertigung bietet der Automobilindustrie eine neue Chance. Die Integration fortschrittlicher Technologie und Digitalisierung ist entscheidend für die Nachhaltigkeit in der Fertigung und fördert Produktivitätssteigerungen, Abfallmanagement und Wettbewerbsvorteile. Durch den Einsatz von KI-gesteuerten Analysen können Prozesse gestrafft, Verschwendung minimiert und Ressourcen optimiert werden, während gleichzeitig ein besserer Einblick in die Produktionsabläufe gewährt wird. Mit diesen Daten können Unternehmen die Produktion optimieren, die vorausschauende Wartung verbessern und den Energieverbrauch senken.
Die nahtlose Integration von IoT-Sensoren, künstlicher Intelligenz und Datenanalyse bietet großen Erstausrüstern (OEMs), die ihre Fertigung an Zulieferer auf der ganzen Welt auslagern, Echtzeiteinblicke in die Leistung der ausgelagerten Werkzeuge und die Produktionseffizienz. Dieser datengesteuerte Ansatz steigert die betriebliche Exzellenz und vergrößert die Auswirkungen von Nachhaltigkeitsbemühungen, indem er Abfallreduzierung, präzise Materialnutzung und proaktive Wartung ermöglicht.
Verantwortungsbewusste Beschaffung erweist sich auch als ein entscheidendes Element zur Förderung nachhaltiger Praktiken. Führungskräfte in der Automobilindustrie erhalten durch die Digitalisierung von Werkzeugen wertvolle Einblicke in die Leistung und Einhaltung von Vorschriften durch die Zulieferer. Forschung von Capgemini zeigt, dass 62% der Automobilunternehmen inzwischen umfassende Nachhaltigkeitsstrategien mit klar definierten Zielen verfolgen, was die zunehmende Bedeutung einer nachhaltigen Beschaffung in der Branche unterstreicht. Durch die Priorisierung von Partnerschaften mit umweltbewussten Zulieferern können Automobilunternehmen ihre Beschaffungspraktiken mit Initiativen zur sozialen Verantwortung und mit Nachhaltigkeitszielen in Einklang bringen und so eine grünere und sozial verantwortliche Zukunft fördern.
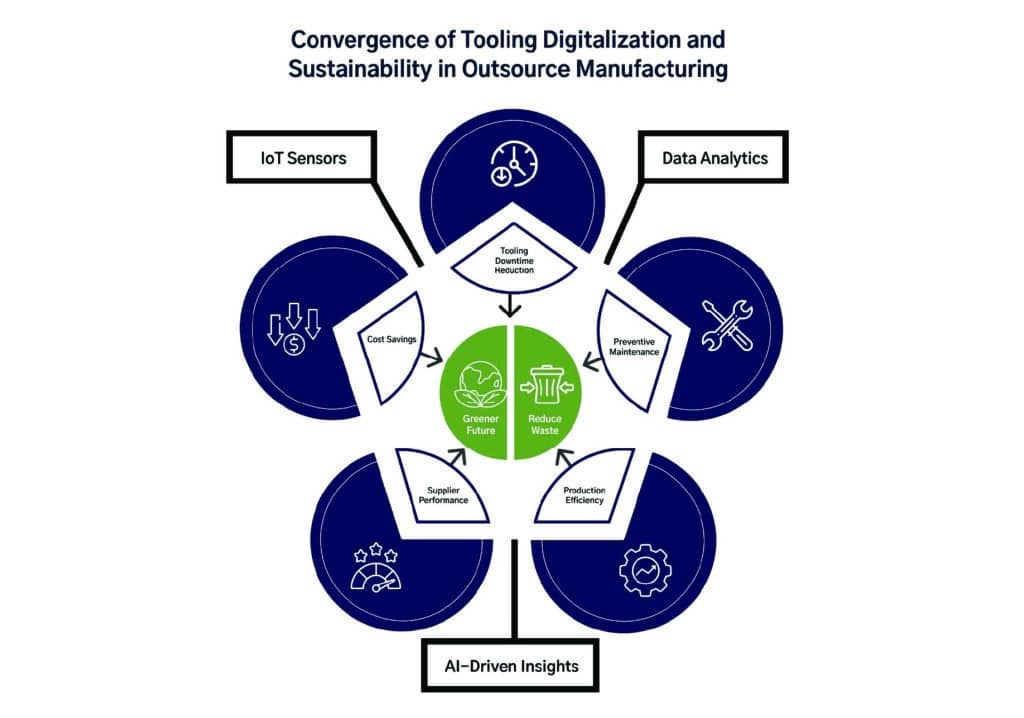
Erfolgsgeschichte aus der Praxis
Die Digitalisierung des Werkzeugbaus treibt die nachhaltige Fertigung in der Automobilbranche voran
Führende Automobilunternehmen, die diesen transformativen Ansatz verfolgen, haben bereits messbare Ergebnisse erzielt, die die Machbarkeit der Synergie zwischen Werkzeugdigitalisierung und nachhaltiger Fertigung bestätigen. Eines dieser Unternehmen ist ein bekannter deutscher multinationaler Automobilzulieferer, der diesen Erfolg mit bedeutenden Fortschritten bei der Werkzeugdigitalisierung und der Nachhaltigkeit vorlebt. Durch die Integration fortschrittlicher Technologien und datengestützter Erkenntnisse, die Optimierung von Abläufen und die Ausrichtung auf eine umweltfreundlichere Zukunft hat das Unternehmen bemerkenswerte Ergebnisse erzielt.
Durch die Digitalisierung der Werkzeuge erhielt das Wartungsteam des Unternehmens einen noch nie dagewesenen Einblick in die vorbeugende Instandhaltung, der es mit Echtzeitdaten und rechtzeitigen Warnmeldungen für proaktive Maßnahmen versorgte. Dieser Ansatz verringerte die Ausfallzeiten der Werkzeuge erheblich, was die Produktivität und die Kosteneinsparungen verbesserte. Darüber hinaus führte der proaktive Wartungsansatz des Unternehmens zu erheblichen Kostensenkungen im Zusammenhang mit Qualitätsproblemen, da durch rechtzeitiges Eingreifen und den Erhalt der Werkzeugintegrität Produktdefekte und kostspielige Nacharbeiten eingedämmt und die Produktqualität insgesamt erhöht werden konnten. Das Unternehmen konnte seine Fertigungsprozesse durch die Analyse historischer Daten und Leistungstrends verfeinern und so die Wahrscheinlichkeit von Fehlern und Mängeln in der Produktionslinie verringern. Dieser datengesteuerte Instandhaltungsansatz optimierte die Werkzeugleistung und trug zur Abfall- und Ressourcenreduzierung bei, was sich perfekt mit dem verantwortungsvollen Abfallmanagement und den allgemeinen Nachhaltigkeitszielen vereinbaren ließ.
Darüber hinaus führte das Engagement des Unternehmens für die Digitalisierung von Werkzeugen zu einer verbesserten Energieeffizienz während der Fertigungsprozesse. Dank der vorausschauenden Wartungsfunktionen der Lösung werden die Werkzeuge im Voraus angemessen gewartet und gepflegt, um Ausfälle zu vermeiden. Dieser proaktive Ansatz minimiert ungeplante Ausfallzeiten, die sonst zu Energieverschwendung während der Leerlaufzeiten führen würden. Infolgedessen konnte das Unternehmen seinen Energieverbrauch und die damit verbundenen Kohlendioxid-Emissionen senken und damit einen wichtigen Beitrag zu seinen Bemühungen leisten, seinen ökologischen Fußabdruck zu minimieren. Durch die Ausschöpfung des vollen Potenzials seiner Werkzeuge durch die Digitalisierung hat das Unternehmen sein unermüdliches Engagement für die Verringerung der Umweltauswirkungen und den Wandel unter Beweis gestellt und seinen Weg zu einer nachhaltigen Produktion weiter gefestigt.
Entdecken Sie unsere verwandten Beiträge
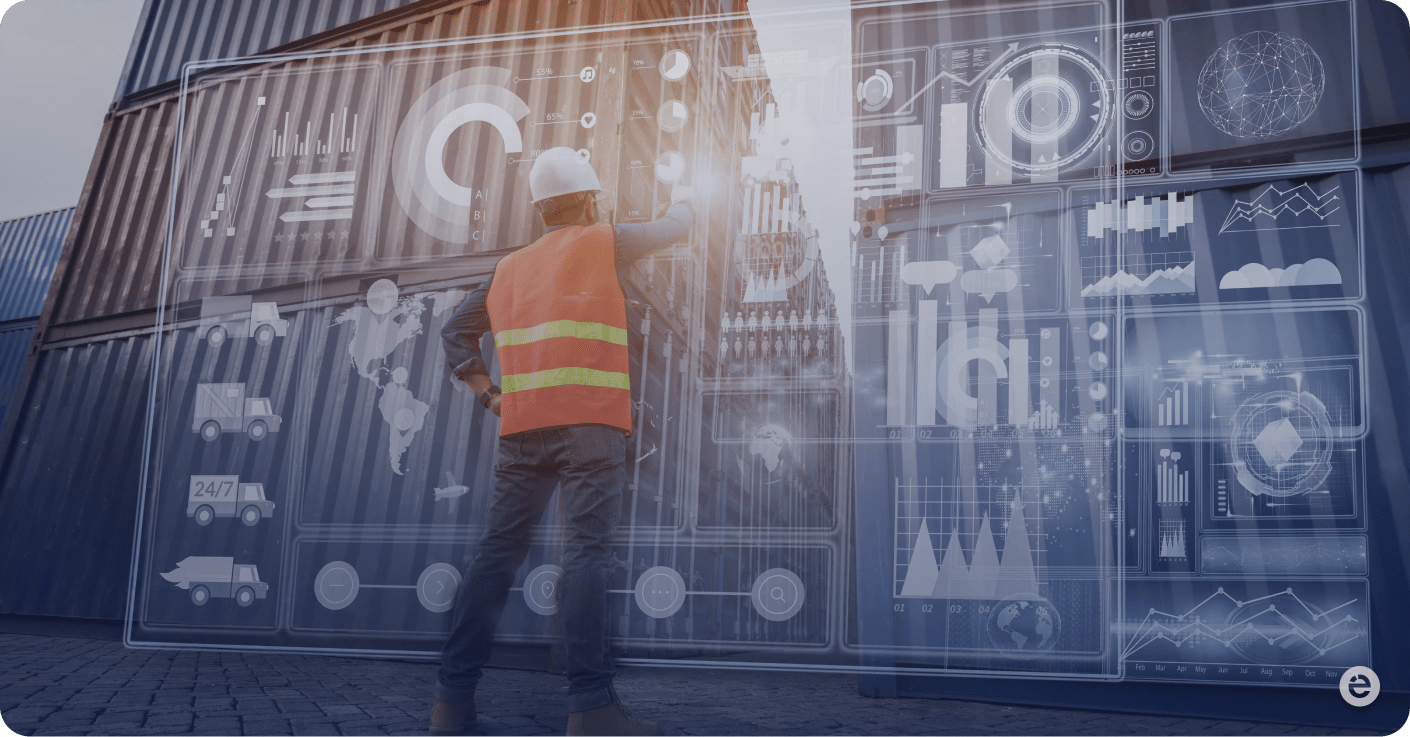
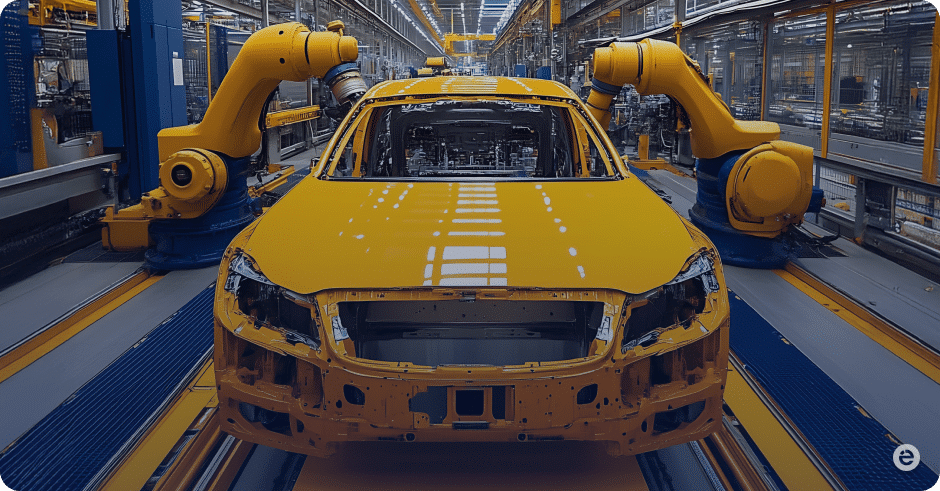
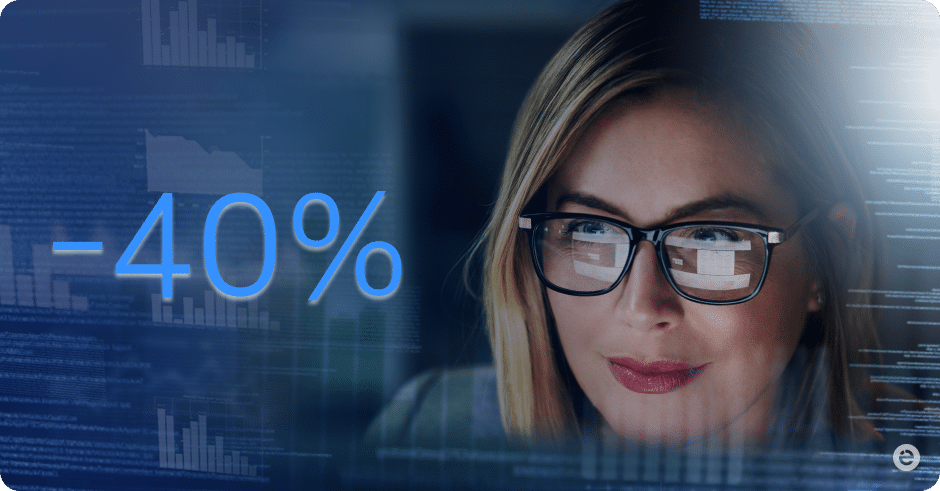
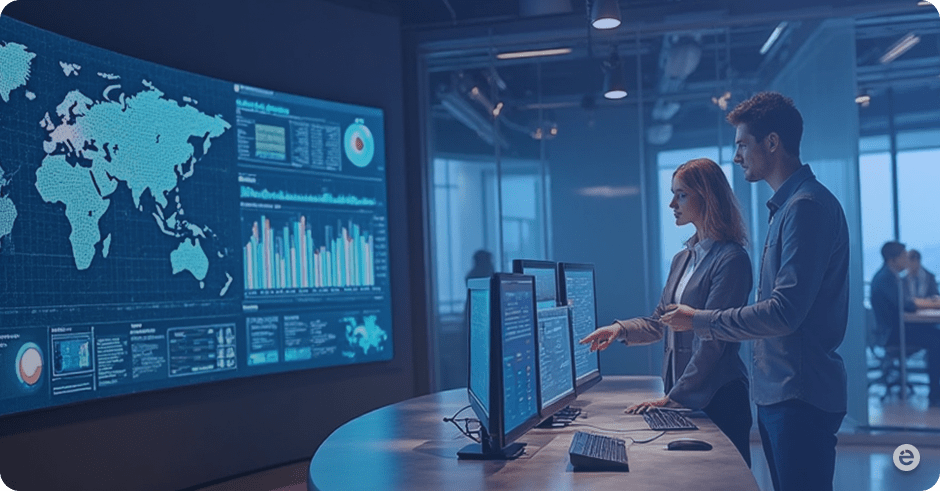
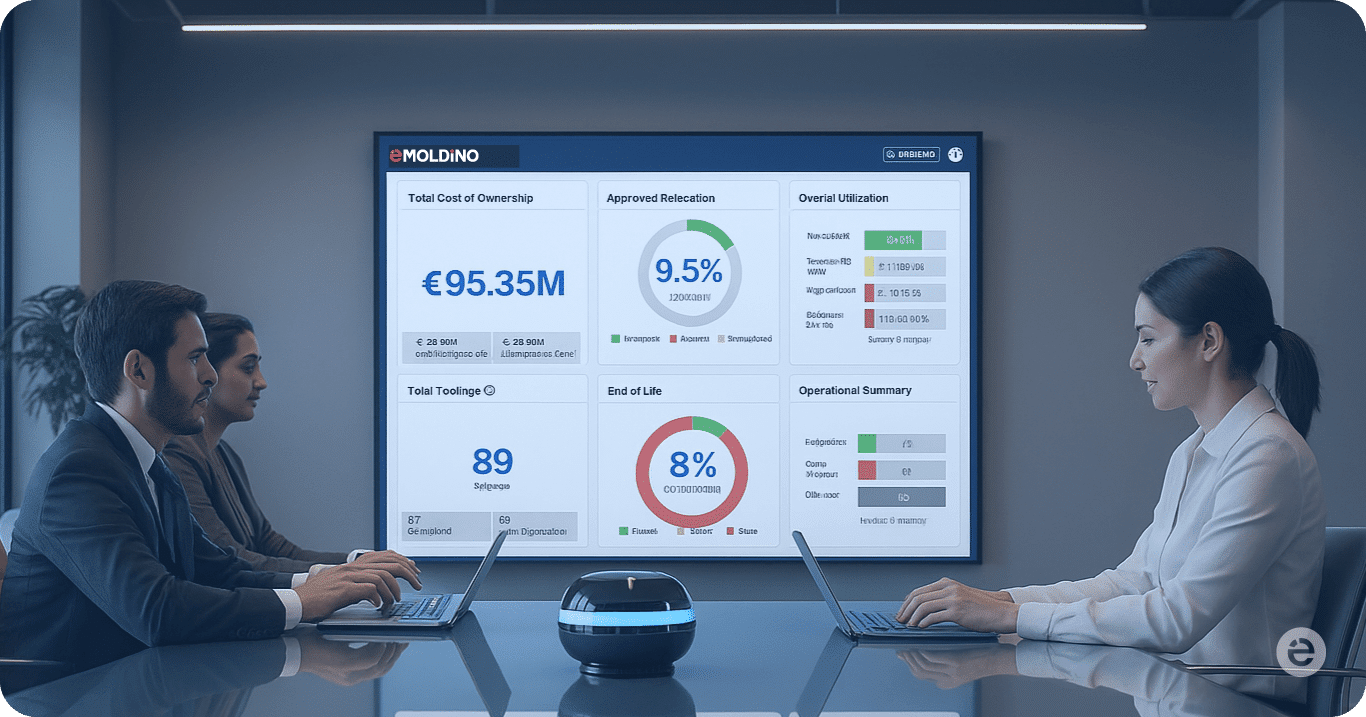
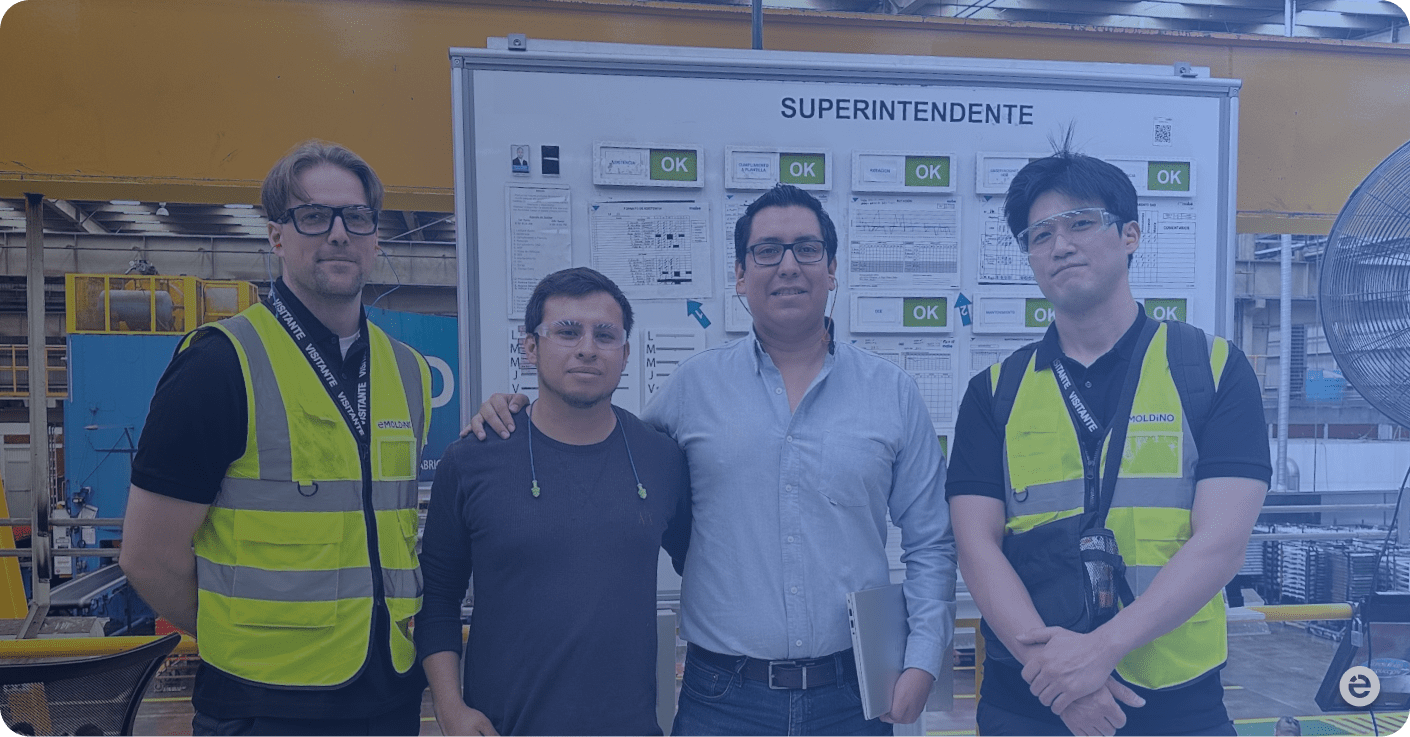
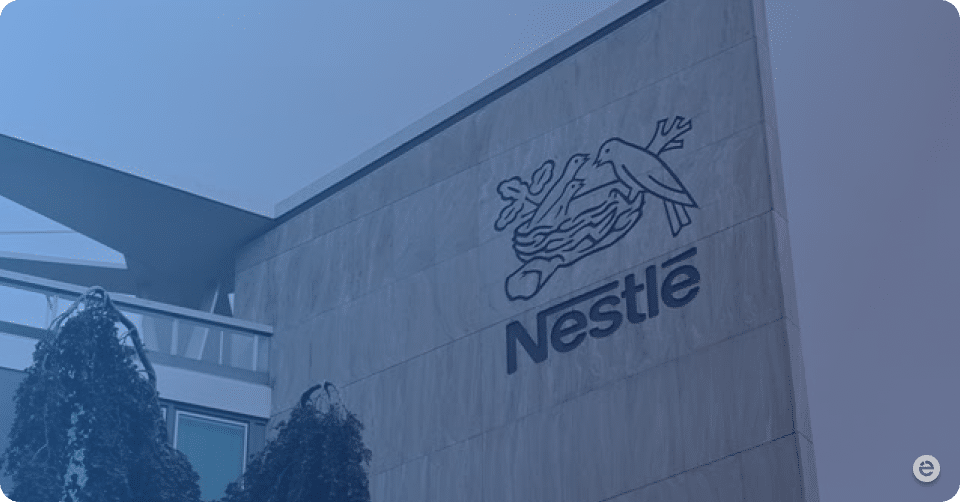
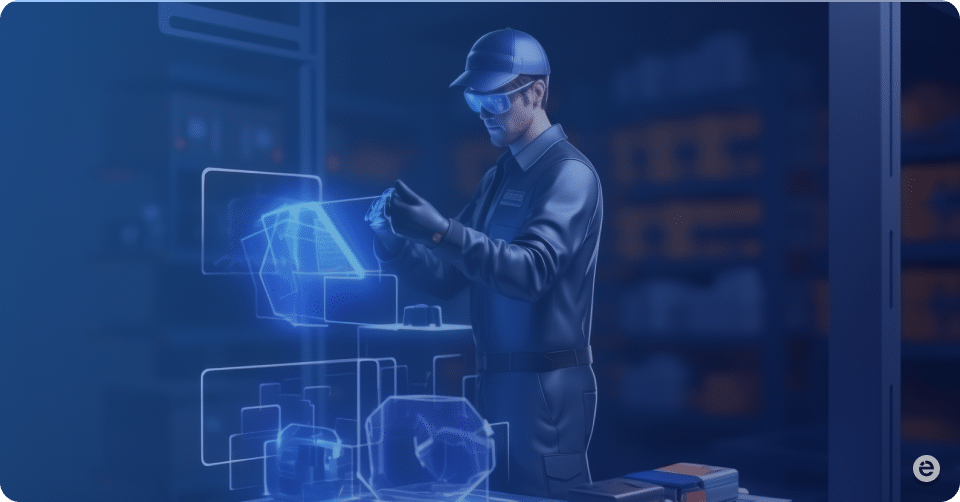
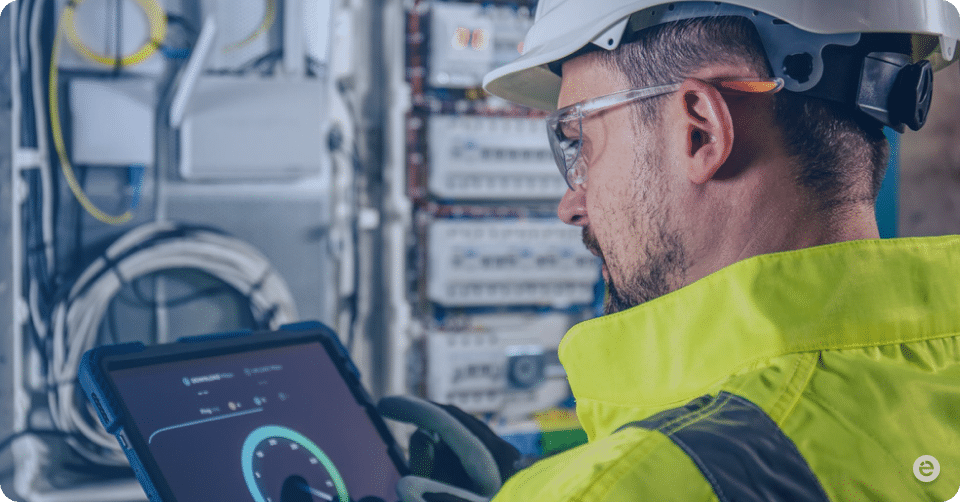
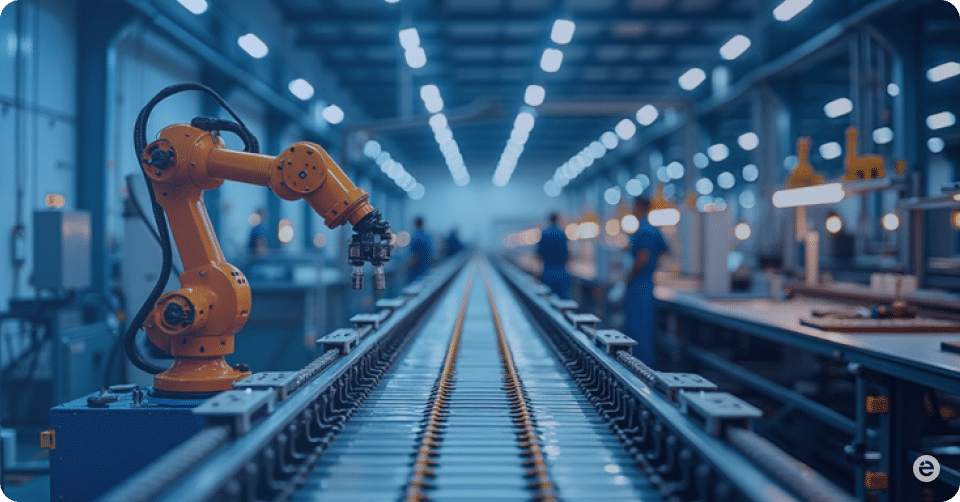