OTHERS
Balancing Cost and Efficiency in Tooling Management and Procurement
2024.03.21
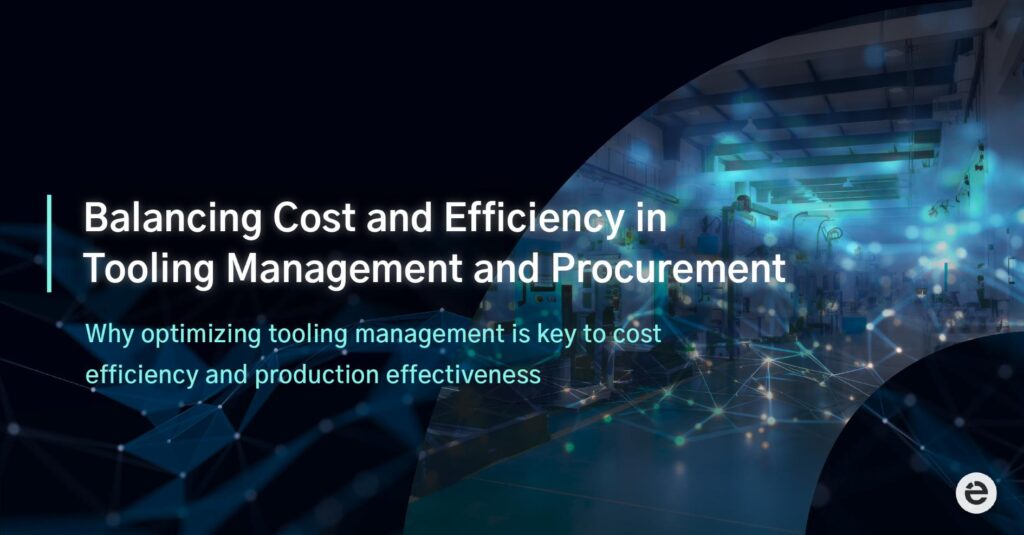
Executive Summary
In outsourced manufacturing, Original Equipment Manufacturers (OEMs) face a difficult challenge in tooling procurement, often alternating between excess and shortage due to a lack of precise lifespan information. This challenge is compounded by the tooling warranty paradox, where tooling fail prematurely, leading to production halts and financial burdens. An emerging tooling digitalization solution is bridging this gap, offering deeper insights into tooling lifecycle usage. This advancement has the potential to reduce tooling purchases by 0.15%, equating to savings of up to $59 million. Moreover, optimizing tooling lifespan to align with warranty periods can yield additional savings of around $7.5 million. Enhanced tracking and management capabilities of this digital system can further mitigate costs related to lost tooling, potentially saving up to $30 million. Ultimately, the adoption of digital tooling management solutions is proving crucial for improving operational efficiency and financial performance in the outsourced manufacturing sectors.
The Dilemma of Tooling Quantification – Too Many or Too Few?
In outsourced manufacturing, a critical and often understated challenge is the management and procurement of tooling. This balancing act, crucial in operational strategy, hinges on a fundamental question: Are Original Equipment Manufacturers (OEMs) purchasing too many or too few tooling? The answer, while seemingly straightforward, is complicated by various underlying factors.
Navigating the Tooling Lifespan and Information Gap
At the heart of this dilemma lies an information gap concerning tooling lifespan. Companies often struggle with limited insights into when tooling will require replacement, leading to two primary issues: production efficiency disruptions and financial planning complications. Unpredictable tooling failures cause unplanned production stops and necessitate frequent tool replacements, making it challenging to budget for tool procurement. This results in either an excess or deficit of tooling misaligned with actual production needs.
Moreover, traditional budgeting practices, which often rely on historical procurement levels without considering discrepancies with current production capacity, exacerbate this problem. The financial implications are significant, including direct impacts on capital expenditure and indirect effects on the cost per part. Additionally, unused tooling represents a financial drain, not only in terms of tied-up capital but also through depreciation. Many companies also adopt a precautionary approach, maintaining a surplus of tools to navigate uncertain production demands. Although this approach provides a safety buffer, it leads to the allocation of capital in assets that are not fully utilized.
In response to these challenges, a transformative solution has emerged in the form of tooling digitalization. eMoldino solution provides procurement managers with comprehensive information on all tooling nearing the end of their lifecycle, enabling strategic decision-making around budgeting, replacements, or refurbishments. Automotive clients utilizing the Tooling Lifecycle feature of the solution have experienced reduced unplanned downtime, more accurate budgeting for tooling procurement, and maximized tooling usage. Overall, clients have significantly reduced production costs through more effective budgeting, fewer purchases of new molds and optimized maintenance schedules.
The Tooling Warranty Paradox in Outsourced Manufacturing
The tooling warranty paradox presents a significant challenge, contrasting sharply with the assurances of warranty terms. This phenomenon, where toolings fail prematurely despite warranty guarantees, disrupts manufacturing processes and prompts a reevaluation of the entire tooling strategy. Key to this paradox is the often neglected aspect of regular maintenance. Insufficient maintenance markedly shortens tooling life, leading to failures before the anticipated warranty period. Additionally, when tooling are pushed beyond their intended capacity, they suffer from excessive wear. This mismatch between actual usage and warranty expectations disrupts operations and necessitates a rethinking of warranty applicability in real-world scenarios. The financial repercussions of this paradox extend beyond the immediate need for additional capital expenditure on tool replacement. The urgency of replacing failed toolings often leads to expedited procurement processes, incurring hidden costs like premium pricing and faster shipping charges. Beyond these direct financial implications, there are broader consequences. Production delays due to tooling failures ripple through the manufacturing process, impacting sales, revenue and the company’s reputation for reliability and quality in a competitive market.
To address the issue of premature tooling failure. executives are increasingly turning to digitalization solutions for tooling management. These solutions offer in-depth analysis of tooling usage, enabling them to identify tooling at risk of excessive use. Additionally, they facilitate comparative benchmarking across different suppliers, enhancing decision-making processes in tooling management. These insights are crucial for optimizing tooling life and ensuring each tooling delivers its intended value.
Moreover, the solutions’ ability to autonomously generate maintenance work orders marks a revolution in traditional maintenance practices. With access to comprehensive historical tooling data, plant engineers can effectively assess and address maintenance needs, updating tool status in real-time post-maintenance practices. This approach reduces unplanned downtimes, on-time availability of capacity, and ensures consistent and efficient production flow.
The Lost Tooling Conundrum
In many facilities, the tracking of tools is still predominantly manual, a method similar to decentralized maintenance teams in other industries, leading to notable inefficiencies. Infrequently used or less visible tooling often become ‘overlooked and forgotten’. The cost implications are substantial, with time spent retrieving misplaced tools directly impacting financial resources. Additionally, the premature replacement of tools due to misplacement parallels unnecessary capital expenditures seen in other industries when assets are presumed lost or non-functional.
Addressing this challenge, a tooling digitalization platform introduces a comprehensive solution with its Tooling Audit feature. This feature integrates Tooling Distribution, Utilization and Operating Status for a complete tooling overview. It not only locates each tool but also tracks its historical movements across different plants or within the plant (from production bay to maintenance bay), providing vital insights into the last usage and location of tooling. This capability is crucial in preventing production disruptions due to missing tools and enhances resource planning and coordination across supplier sites.
The benefits of this approach are multi-faced. By reducing the frequency of tool misplacement, companies can diminish the need for new tool procurement, thereby saving costs. Moreover, a well-managed tool distribution system helps mitigate the risk of counterfeit tools infiltrating the production process, thus safeguarding quality and reputation.
Real-World Impact
eMoldino’s solution has demonstrated its effectiveness in substantial tooling management challenges, illustrated by two client cases. In the first case, a client discovered unauthorized use of a tool moved from the EU to South America, leading to counterfeiting issues and the need for new tooling. This situation highlighted the potential for significant revenue recovery through reducing counterfeits, with possible recoverable sales up to $1,950,000, depending on the company’s sales volume. The second case involved an unexpected tool relocation from the EU to the USA, which the OEM was unaware of, causing delays in meeting a sudden demand surge. By adopting eMoldino tooling solution, the client was able to prevent unauthorized tool movements, significantly reducing risks associated with tool misplacement, counterfeiting and delayed market response.
Talk to us or explore our blogs to learn more.
Explore Our Related Posts
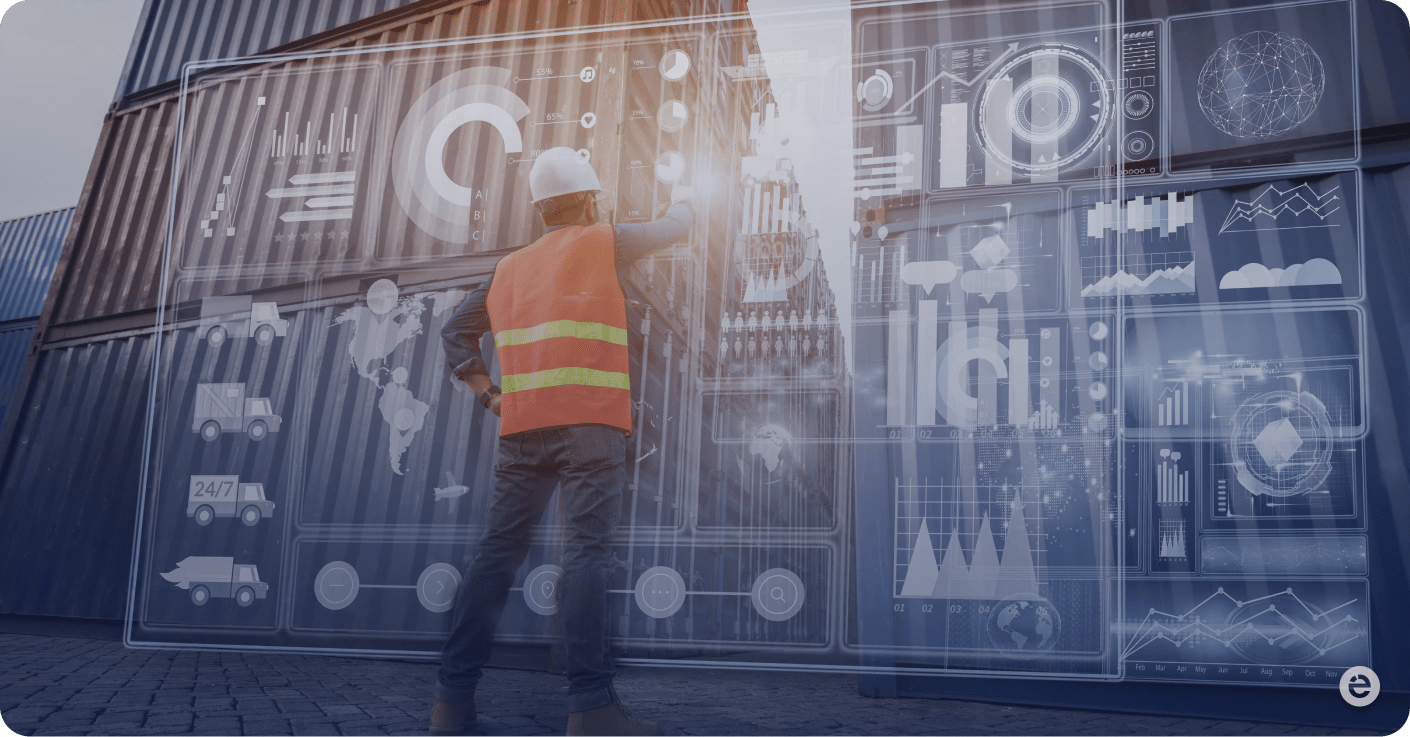
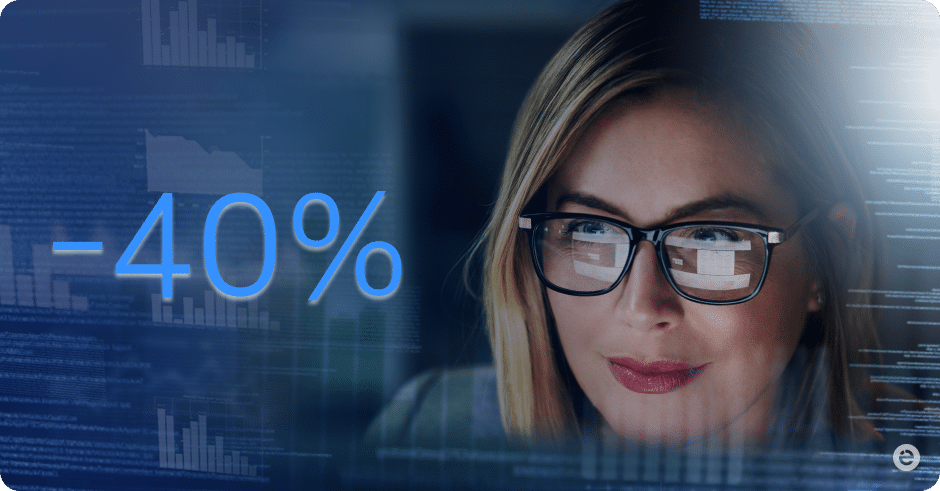

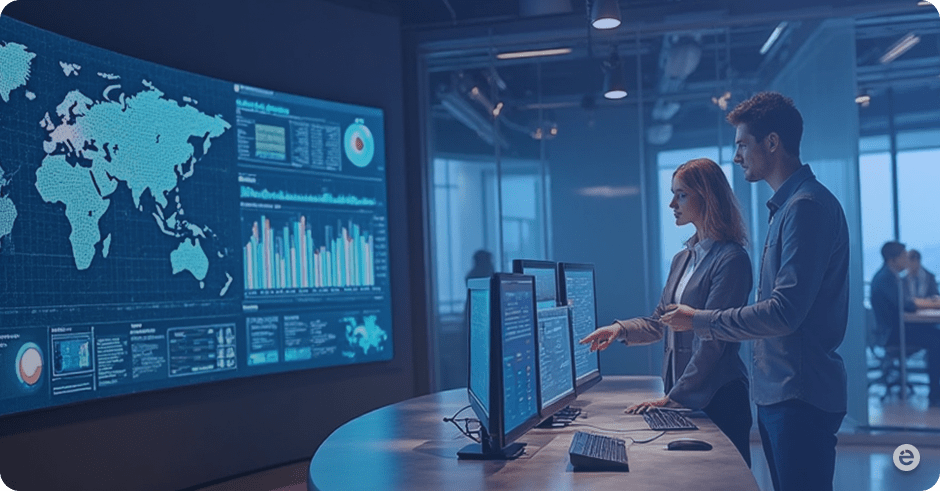
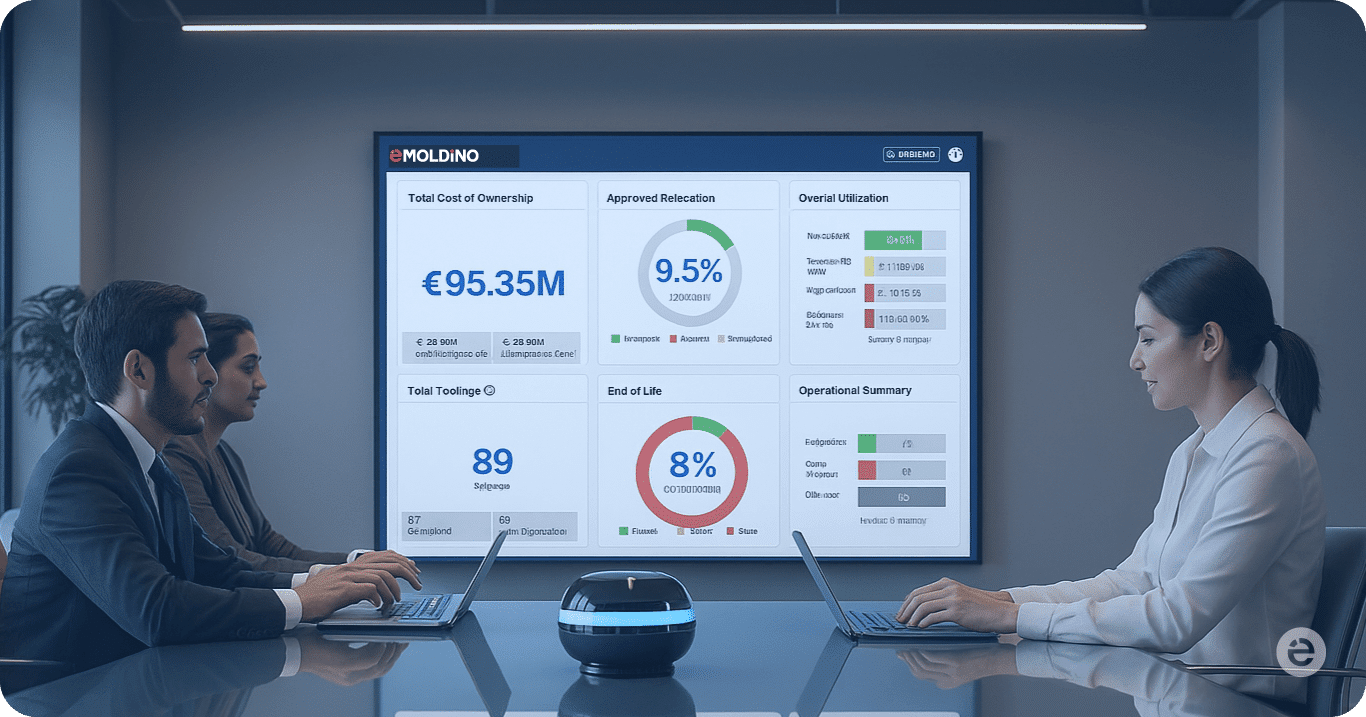
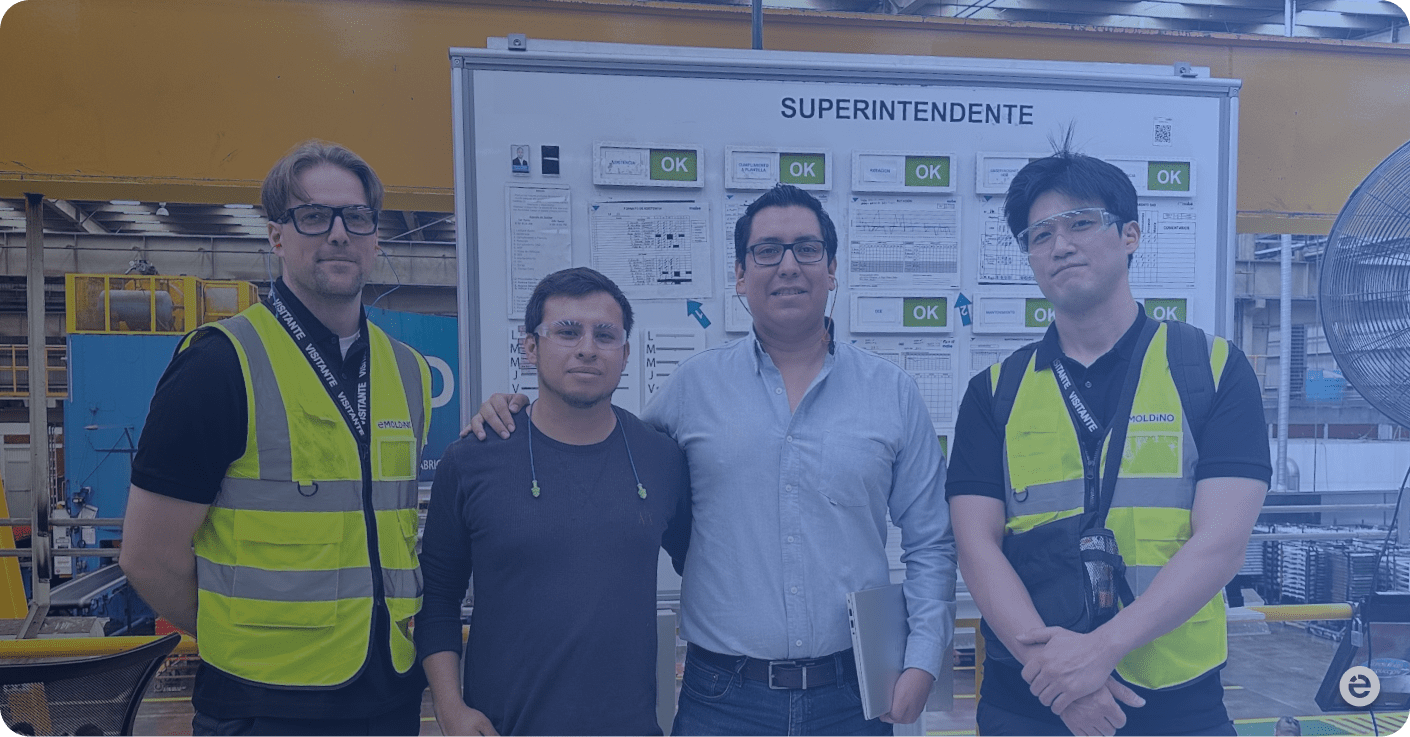
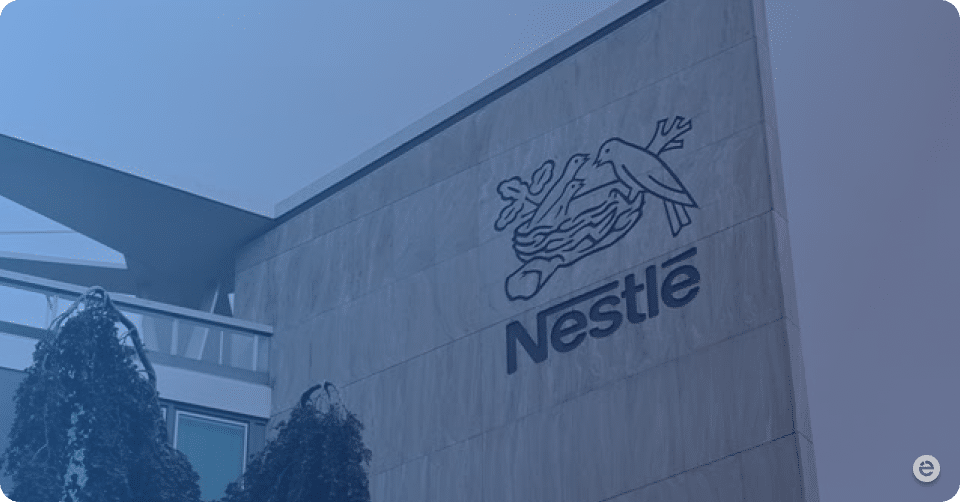
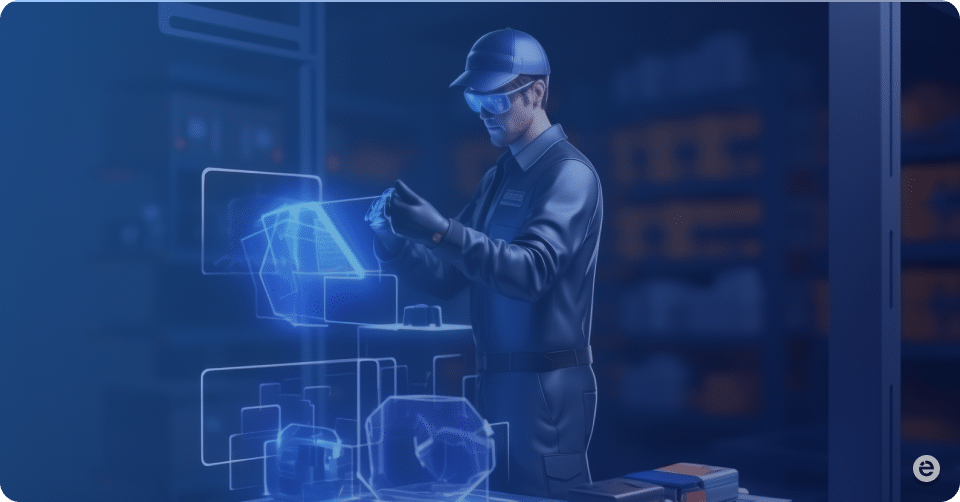
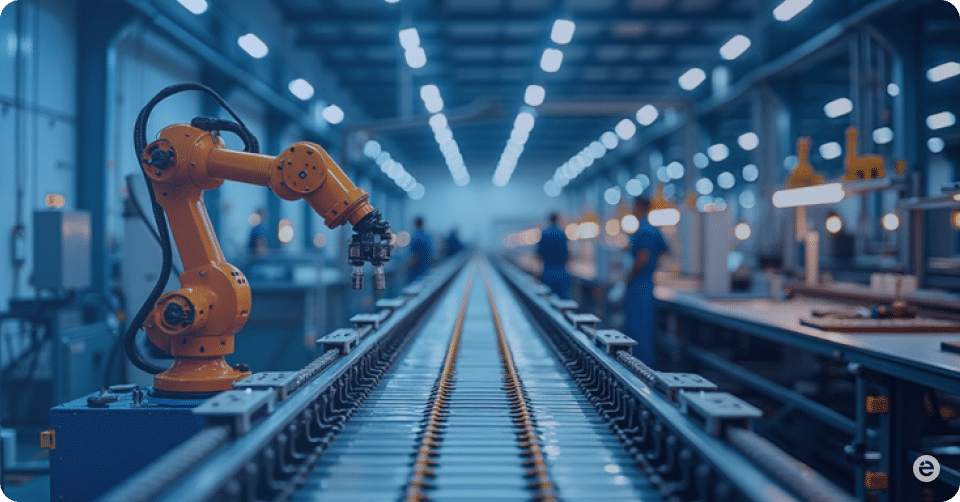
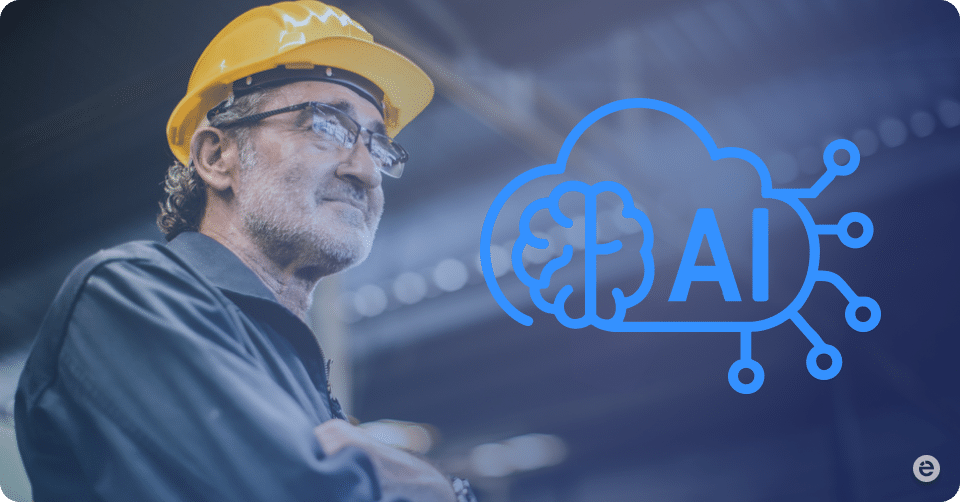
Wow, incredible blog layout! How long have you been blogging
for? you make blogging look easy. The overall look of your web site is
magnificent, as well as the content!